Innovative Technologie definiert den Verbrennungsmotor neu
Der Verbrennungsmotor
Seit seiner Einführung im späten 19. Jahrhundert hat der Verbrennungsmotor eine der beeindruckendsten Entwicklungen in der Geschichte der Technologie durchlaufen. Er revolutionierte die Automobilindustrie, eröffnete Milliarden von Menschen neue Möglichkeiten der Mobilität und schuf die Grundlage für den modernen Verkehr. Dank bahnbrechender Innovationen wie der Einspritztechnologie, der Turboaufladung und fortlaufender Effizienzsteigerungen hat der Verbrennungsmotor im Laufe der Jahrzehnte seine Leistungsfähigkeit gesteigert und zugleich seine Umweltverträglichkeit kontinuierlich verbessert.
Trotz dieser Errungenschaften steht der Verbrennungsmotor nun vor einer entscheidenden Wende. Angesichts der globalen Bemühungen um Klimaschutz und der Einführung von strengen Emissionsvorschriften wird der Verbrennungsmotor zunehmend in Frage gestellt. Die Diskussion um das Verbot von Neuwagen mit Verbrennungsmotoren in vielen Ländern hat zu einem Paradigmenwechsel in der Automobilindustrie geführt.
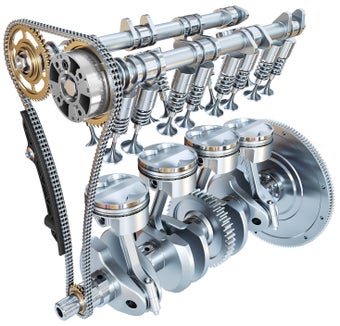
Der Verbrennungsmotor,
ein legendäres technisches
Meisterwerk - Milliardenfach bewährt
Der elektrische Antrieb
Der elektrische Antrieb, gespeist durch Batterien, gilt als Schlüsseltechnologie, um den Verbrennungsmotor langfristig zu ersetzen und in Kombination mit erneuerbaren Energien die CO2-Emissionen nahezu auf null zu reduzieren. Elektroantriebe nutzen Energie weitaus effizienter, mit Wirkungsgraden von über 90%, während die meisten in Betrieb befindlichen Verbrennungsmotoren oft nur 20–30% erreichen. Dies macht den elektrischen Antrieb ressourcenschonender und prädestiniert für eine nachhaltigere Mobilität.
Während elektrische Antriebe in den letzten Jahren zunehmend für die Mobilität der Zukunft angesehen werden, gibt es aber immer mehr berechtigte
Kritikpunkte, die nicht außer Acht gelassen werden dürfen. Die Produktion von
Lithium-Ionen-Batterien ist ressourcenintensiv und mit erheblichen Umwelt- sowie sozialen Problemen durch den Abbau von Rohstoffen wie Lithium, Kobalt und Nickel verbunden. Zudem belastet die energieintensive Batterieproduktion die CO2-Bilanz der Fahrzeuge, wodurch der Umweltvorteil erst über längere
Nutzungsdauer zum Tragen kommt.
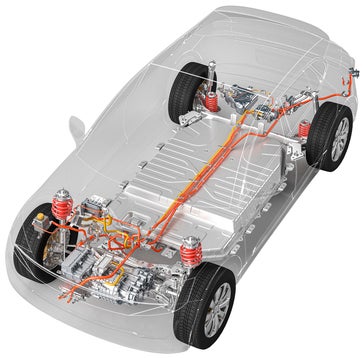
Der elektrische Antrieb im Auto
Elektrofahrzeuge sind nur so sauber wie der Strom, mit dem sie betrieben werden!
Ein weiterer sehr kritischer Punkt ist die Abhängigkeit der Umweltbilanz von der Stromquelle. In sehr vielen Ländern mit einem hohen Anteil fossiler Energien fällt die Klimabilanz von Elektrofahrzeugen deutlich schlechter aus. Zusätzlich fehlen effiziente Recyclingverfahren für Batterien, was langfristig zu großen Mengen an Elektroschrott führen könnte.
Praktische Einschränkungen im täglichen Einsatz
Elektroautos bieten im Schnitt Reichweiten von 300 bis 500 Kilometern, was für Stadt- und Pendelverkehr ausreicht, jedoch bei langen Fahrten problematisch wird. Kalte Temperaturen, die Nutzung von Heizung oder Klimaanlage und hohe Reisegeschwindigkeiten reduzieren die Reichweite erheblich.
Auch das hohe Eigengewicht der Fahrzeuge stellt ein Problem dar. Es schränkt sowohl die Nutzlast als auch den Einsatz für gewerbliche Zwecke ein, insbesondere bei Fahrzeugen mit Anhängern oder schweren Beladungen. Auf langen Strecken und für Transporte bleibt die Elektromobilität somit oft hinter den Möglichkeiten von Verbrennungsmotoren zurück.
Eine Zweit- oder Drittnutzung von Elektrofahrzeugen, wie sie bei Verbrennerfahrzeugen gängig ist, wird durch eine hohe Kostenbetrachtung für den Austausch der Batterie deutlich unattraktiver. Diese finanzielle Hürde stellt für potenzielle Käufer gebrauchter Elektroautos einen erheblichen Nachteil dar und erschwert eine langfristige Nutzung über mehrere Fahrzeugbesitzer hinweg.
Insgesamt zeigt sich, dass die Elektromobilität viel Potenzial bietet, jedoch noch wesentliche Herausforderungen bei Batterietechnologie, Infrastruktur, Recycling, Wirtschaftlichkeit und praktischer Nutzbarkeit überwunden werden müssen, um eine umfassende Alternative zu herkömmlichen Antrieben zu werden.
Diese in den vergangenen Jahren gesammelten Erfahrungen mit der Elektromobilität stehen zunehmend im Widerspruch zu den ursprünglichen ideologischen Vorstellungen, die diese Technologie politisch vorantreiben sollten. Immer mehr Stimmen plädieren für eine größere Technologieoffenheit und fordern sogar eine Aufhebung des ab 2035 geplanten Verbrennerverbots. Die Begrenzung technologischer Möglichkeiten durch politische Vorgaben wird immer deutlicher kritisch hinterfragt. Ein Umdenken scheint geboten, wie die Erfahrungen der letzten Jahre deutlich gemacht haben.
Neue technologische Ansätze!
Wenn eine Technologie neu konzipiert wird und durch innovative Änderungen sowohl ihre Effizienz als auch ihre Leistungsfähigkeit gesteigert werden kann, eröffnen sich möglicherweise auch völlig neue Ansätze und Perspektiven.
In diesem Kontext könnte die Vorstellung eines neuartigen Verbrennungsmotor-Konzepts die Diskussion über eine mögliche Überprüfung des Verbrennerverbots zusätzlich an Bedeutung gewinnen.
Die Idee, die durch nachfolgende Beispiele die Machbarkeit und das Potenzial neuer Technologien aufzuzeigen, legt nahe, dass technologische Innovationen nicht nur einseitige Lösungen bieten, sondern auch den Fortschritt anderer umweltfreundlicher Technologien entscheidend vorantreiben können.
Ein neuartiger technologischer Grundbaustein, der im Folgenden näher erläutert wird, soll verdeutlichen, dass pauschale Verbote und politische Ideologien nicht immer der richtige Weg sind, um eine nachhaltige Zukunft zu gestalten. Vielmehr setzt die Vielfalt an Technologiemöglichkeiten Maßstäbe, die gemeinsam zu einer signifikanten Verbesserung der Umweltbilanz beitragen können.
Vorstellung einer weltneuen Technologie
„Der Kurbelwellen-Ersatz“ oder „Konzept für einen effizienten Verbrennungsmotor, der Rotationskolbenmotor"
“
Schauen Sie am besten zuerst das Video an – so werden die technischen Erklärungen danach leichter verständlich!
Vorteile durch den Ansatz einer neuen Motorarchitektur
Diese Präsentation stellt ein Konzept für einen Verbrennungsmotor einer neuen Generation vor. Durch den Verzicht auf die klassische Kurbelwelle und die Einführung einer völlig neuartigen Kulissenwelle zur Umwandlung von Wärme- in mechanische Rotationsenergie ergeben sich grundlegende technische Neuerungen. Ziel ist es, den Wirkungsgrad des Verbrennungsmotors signifikant zu steigern, wobei die physikalischen Grenzen des Carnot-Prozesses, der durch Temperaturdifferenzen definiert ist, berücksichtigt werden. Die Tatsache, dass bereits heute reine Verbrennungsmotoren wie Schiffsmotoren oder stationäre Verbrennungsmotoren Wirkungsgrade von über 50 % erreichen, zeigt das Potenzial dieses Konzepts, ähnliche Effizienzsteigerungen zu realisieren und möglicherweise sogar zukünftige Erwartungen zu übertreffen. Zum besseren Verständnis der neuartigen Technologie sollte das Erklärungsvideo begleitend angeschaut werden.
Rotationskolbenmotor vs. Kurbelwellenmotor
Thema 1: Architekturunterschiede
Geometrie der neuartigen Kulissenwelle
Im Unterschied zur Kurbelwelle eines klassischen Verbrennungsmotors ist die neuartige Kulissenwelle des neuen Rotationskolbenmotors etwas komplexer aufgebaut.
Eine erste Lagerscheibe 1 treibt eine erste Welle an. Diese erste Welle (Abtriebswelle) hält die Lagerschale 1 symmetrisch zur Wellenachse ausgerichtet und gewährt einen präzisen Rundlauf. Auf der Lagerscheibe 1 sind 4 Lagerbuchsen symmetrisch angeordnet, von denen 2 Lagerbuchsen in die auslaufenden Enden zweier Kulissenbahnen einer ersten Steuerscheibe 1 eingreifen, die freilaufend auf einer zweiten Welle drehbar gelagert ist. Steuerscheibe 1 und Lagerscheibe 1 sind so zueinander angeordnet, dass die beiden Wellenachsen in Verbindung mit der beschriebenen Lagebuchsen-Kulissenbahn Verbindung zwei gespiegelte gleichschenklige rechtwinklige Dreiecke abbilden. Siehe hierzu Bild 1.
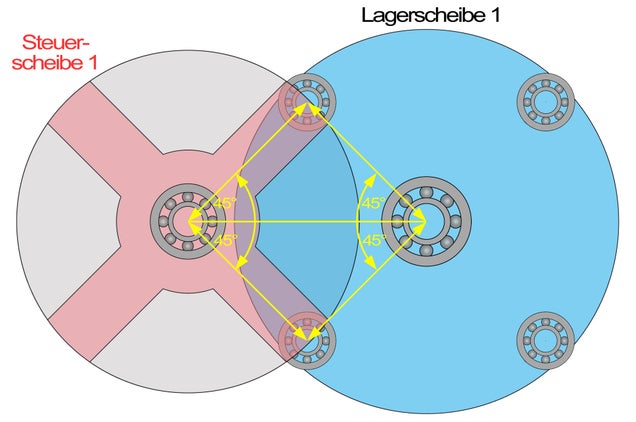
Bild 1
Auf den Steuerscheibe 1+2 sind insgesamt
je 4 Kulissenbahnen symmetrisch angeordnet.
Drehen sich die Lagerscheibe 1+2 über die Abtriebswelle um 45° im Uhrzeigersinn, dann folgt nur eine Lagerbuchse seiner zugeordneten Kulissenbahn, bis diese präzise in der Flucht zwischen den beiden Drehachsen liegt. Ordnet man dem ersten Steuer-/ Lagerscheibenpaar mit einer Phasenverschiebung von genau 45° ein zweites Steuer-/ Lagerscheibenpaar zu, entsteht so die neuartige Kulissenwelle, die das Grundgerüst des Rotationskolbenmotors darstellt.
Siehe hierzu Bild 2a/b.
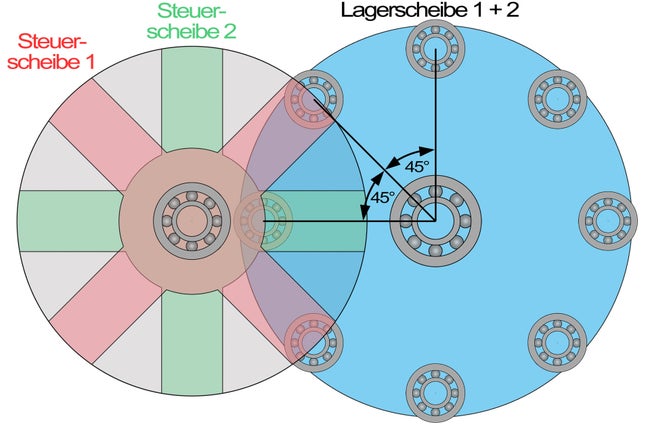
Bild 2a
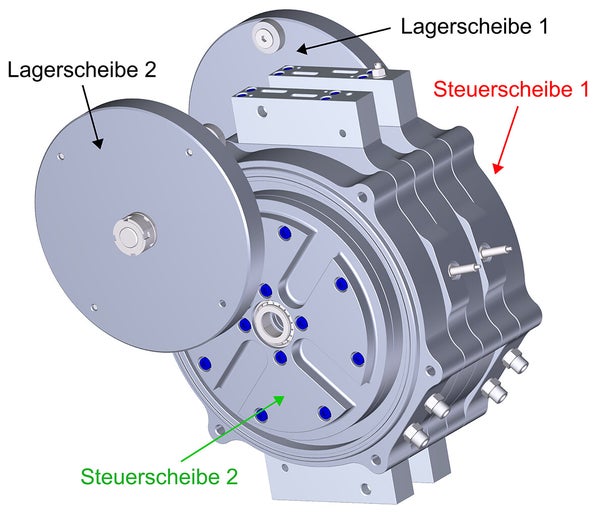
Bild 2b
Wichtig ist, dass die Lagerscheiben 1 + 2 mit ihrer 45° Phasenverschiebung starr mit der Abtriebswelle verbunden sind, während die beiden Steuerscheiben 1 + 2 unabhängig auf der gemeinsamen zweiten Welle drehbar gelagert sind. Durch diese Lagerbuchsen-Kulissenbahn Prinzip wird eine äußerst simple und zugleich
zuverlässige Bauweise erzielt, bei der eine kontinuierliche Rotation der beiden Steuerscheiben 1 + 2 die gewünschten, relativ zueinander verschiedenen und nicht gleichförmigen Bewegungen bewirken. Das Übersetzungsverhältnis eines Steuer-/ Lagerscheibenpaars wird durch die Position des
Lagerbuchsen-Kulissenbahn Prinzips gebildet und verläuft von 0 bis 2,414, oder geometrisch genauer (√2+1).
Diese beschriebene Architektur des neuartigen Rotationskolbenmotors ermöglicht neben einer leichten und kompakten Bauform (vier Kolben auf einer Steuerscheibe) auch eine effiziente Energieübertragung von der Expansion des Verbrennungsvorgangs übertragen über den Kolben hin zum starken Drehmoment an der Abtriebswelle. In jedem Winkelschritt des Arbeitstaktes bilden zwei sich gegenüberliegende Kolben, die mit den Steuerscheiben in fester Verbindung stehen, einen reziproken Betrieb. Der dynamische wechselnde Ablauf aktiver und passiver Kolben überträgt die Kraft vom Kolben auf die Abtriebswelle. Das wechselnde Übersetzungsverhältnis unterstützt diesen Vorgang.
Bild 3 zeigt den Geschwindigkeitsverlauf der beiden Steuerscheiben 1 + 2 (rote und grüne Linie), die in einer 45° Phasenverschiebung abgebildet sind. Beide Steuerscheiben bewegen sich in die gleiche Drehrichtung. Die Geschwindigkeitsunterschiede der beiden Steuerscheiben subtrahieren sich zu einer neuen Relativgeschwindigkeit, die durch die lilafarbige Linie dargestellt wird. Diese gebildete Relativgeschwindigkeit wird in den nachfolgenden Erklärungen als aktive Kolbengeschwindigkeit im Rotationskolbenmotor betrachtet.
Bild 3: Funktionsdiagramm
der Arbeits-Geschwindigkeiten
Steuerscheibe 1
Steuerscheibe 2
Relativgeschwindigkeit
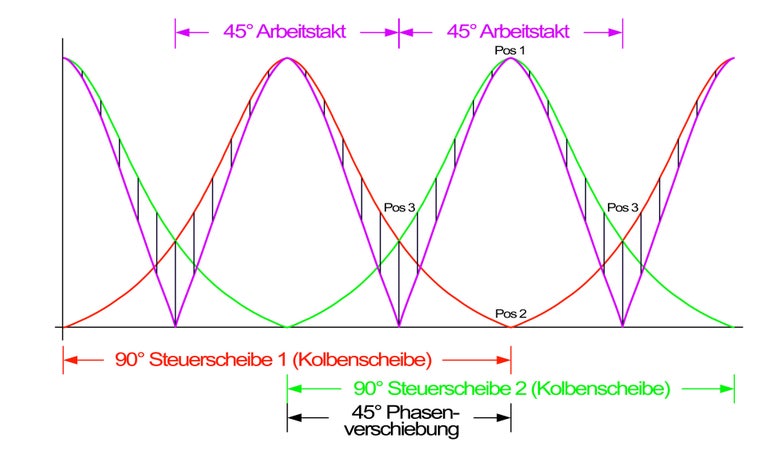
Bild 4:
Perspektivische Darstellung
der beiden Steuerscheiben 1 + 2
in einem 45° Winkelversatz

Bild 5:
Funktionsdarstellung des Rotationskolbenmotors
bei Vmax der 4 Aktiv-Kolben (Pos1 - siehe Bild 3)
und Vnull der 4 Passiv-Kolben (Pos2 - siehe Bild 3)
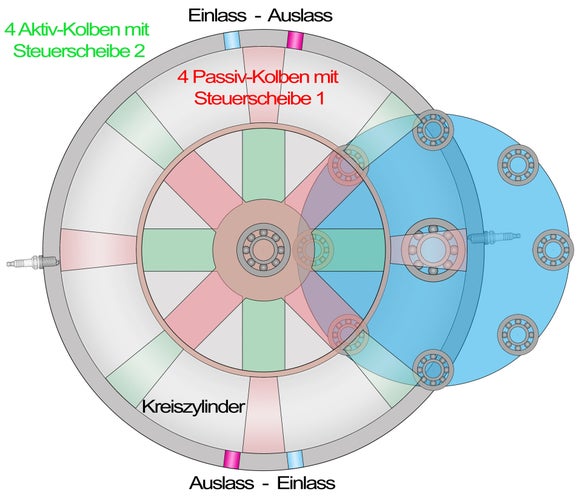
Bild 6:
Funktionsdarstellung des Rotationskolbenmotors
bei Aufgabenwechsel der
4 Aktiv-Kolben und der
4 Passiv-Kolben
(Pos3 - siehe Bild 3)
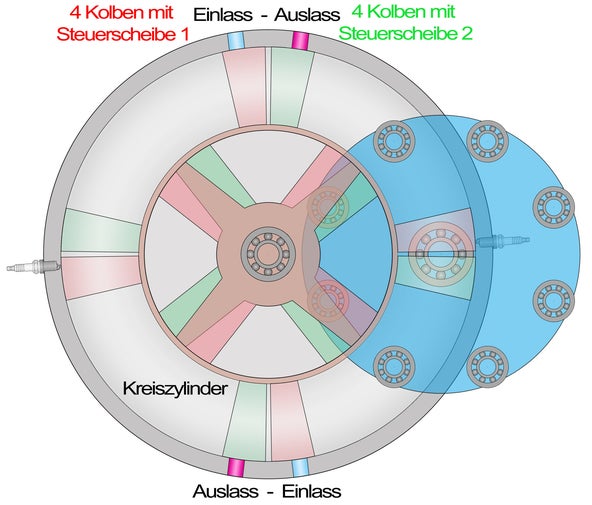
Geometrie der Kurbelwelle
Die Kurbelwelle ist ein wesentlicher Bestandteil nahezu aller Hubkolben-Verbrennungsmotoren und hat sich durch ihre robuste und zuverlässige Funktion über Jahrzehnte bewährt. Ihre Hauptaufgabe besteht darin, die lineare Bewegung der Kolben in eine rotierende Bewegung umzuwandeln und damit das Drehmoment des Motors bereitzustellen.
Die Geometrie der Kurbelwelle beeinflusst maßgeblich die Bewegung des Kolbens im Zylinder. Durch die rotierende Bewegung der Kurbelwelle folgt die Kolbenbewegung einer sinusförmigen Geschwindigkeit. Dies bedeutet, dass die Geschwindigkeit des Kolbens nach dem oberen Totpunkt (OT) zunächst langsam zunimmt, dann bis zu einem Maximalwert in der Nähe der Mitte des Hubs ansteigt und anschließend wieder abnimmt, bis der Kolben den unteren Totpunkt (UT) erreicht. Diese nichtlineare Bewegung (siehe blaue Linie, Abb. 7) resultiert aus der kinematischen Kopplung von Pleuel und Kurbelwelle. Der Pleuelwinkel verändert sich während der Bewegung kontinuierlich, wodurch sich die effektive Hubgeschwindigkeit des Kolbens abhängig vom Kurbelwinkel ändert. Zudem führt die Hebelwirkung des Pleuels auf die Kurbelwelle zu einer variierenden Kraftübertragung, was sich direkt auf das Drehmomentverhalten des Motors auswirkt.
Verbrennungsverlauf im Arbeitstakt (allgemein)
Der Expansionsverlauf in einem Verbrennungsmotor vom oberen Totpunkt (OT) bis hin zum unteren Totpunkt (UT) beschreibt die Phase, in der die Verbrennungsgase nach der Zündung des Gemischs ihre Energie auf den Kolben übertragen. Diese gewonnene mechanische Energie wird unmittelbar auf die Abtriebswelle in Form von Drehmoment und Winkelgeschwindigkeit umgelenkt. Der Druckverlauf in dieser Phase lässt sich in mehrere charakteristische Abschnitte unterteilen:
Phase 1: Maximaldruck direkt nach der Zündung (kurz nach OT)
Nach der Zündung des Kraftstoff-Luft-Gemischs, das in der Regel einige Grad vor dem oberen Totpunkt gezündet wird, kommt es zu einer raschen Verbrennung und einer schnellen Druckerhöhung im Zylinder. Der Druck erreicht seinen Höchstwert, den sogenannten Verbrennungsdruck, kurz nach dem oberen Totpunkt, wenn die Flammenfront das gesamte Gemisch durchwandert hat. Dieser maximale Druck ist sehr hoch und treibt den Kolben mit maximaler Kraft nach vorn.
Phase 2: Expansion mit abnehmendem Druck (von OT in Richtung UT)
Sobald der Kolben seine Vorwärtsbewegung beginnt, dehnen sich die heißen Verbrennungsgase im Zylinder aus. Diese Expansion führt zu einer Abnahme des Drucks, da das Gasvolumen größer wird. Der Druck sinkt dabei in einer typischen exponentiellen Kurve, die von der thermodynamischen Zustandsänderung abhängt. Trotz des sinkenden Drucks bleibt die Kraftübertragung auf den Kolben effizient, da die Druckabnahme vergleichsweise langsam erfolgt.
Phase 3: Ende der Expansion (kurz vor UT)
Gegen Ende des Expansionstakts, wenn der Kolben dem unteren Totpunkt näherkommt, ist der Druck bereits stark gesenkt. Der verbleibende Druck reicht jedoch noch aus, um die Bewegung des Kolbens zu unterstützen, wenn auch mit deutlich verringerter Kraft.
Typische Druckwerte im UT-Bereich liegen deutlich unter dem maximalen Verbrennungsdruck, da die Expansion fast vollständig abgeschlossen ist und die Energie in Form von Arbeit auf den Kolben übertragen wurde. Wie der Verbrennungsdruck im Endstadium gestaltet wird, hängt maßgeblich von den gewünschten Effizienz- oder Leistungsanforderungen ab.
Die Grafik in Bild 7 zeigt den charakteristischen Geschwindigkeitsverlauf am Kolben von OT nach UT. Die rote Linie zeigt die Relativgeschwindigkeit des Kolbens beim Rotationskolbenmotors dar, die blaue Linie zeigt die Kolbengeschwindigkeit des Kurbelwellenmotors.
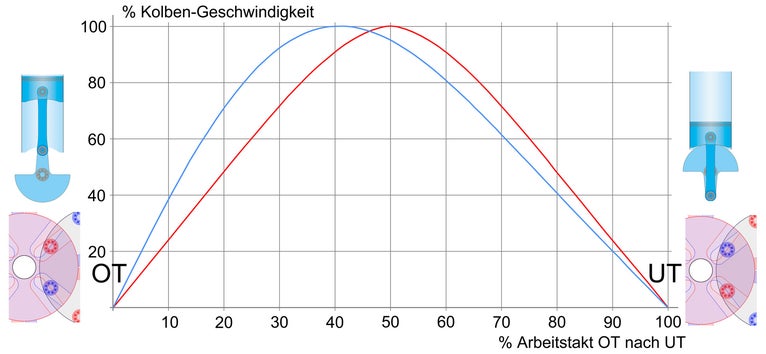
Die Grafik in Bild 8 zeigt einen charakteristischen Drehmomentverlauf an der Abtriebswelle von OT nach UT. Die rote Linie stellt den Verlauf des Rotationskolbenmotors dar, die blaue Linie stellt den Verlauf des Kurbelwellenmotors dar.
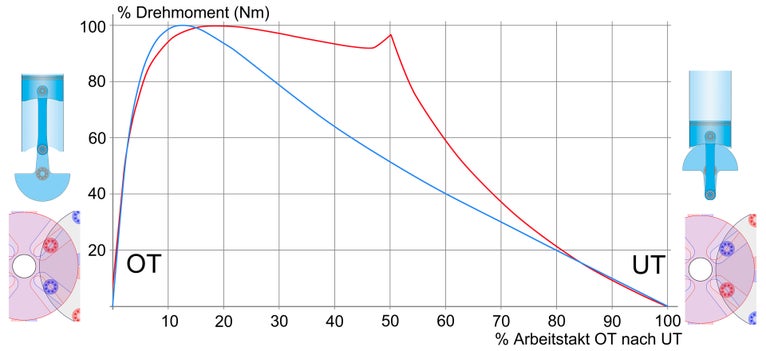
Beide Verläufe entspringen nur einer theoretischen Betrachtung, basierend auf gleichem Kolbendurchmesser, gleichen Hubweg und ungefähr gleichen Expansionsverlauf einer Verbrennungsphase.
Da in einem rotierenden System Drehmoment und Winkelgeschwindigkeit gemeinsam die Leistungsabgabe bestimmen, besteht auch eine feste Beziehung zwischen der Krafteinwirkung auf den Kolben und seiner Geschwindigkeit. Die verrichtete Arbeit beider vergleichenden Systeme bleibt, ohne Einfluss irreversibler Verluste, stets gleich.
Thema 2: Verdichtungsverhältnis
Geometrisches Verdichtungsverhältnis (Verbrennungsmotor allgemein)
Das geometrische Verdichtungsverhältnis eines Motors ist eine feste Größe, die durch die Konstruktion und Architektur des Motors vorgegeben ist. Es beschreibt das Verhältnis zwischen dem gesamten Zylindervolumen, wenn sich der Kolben im unteren Totpunkt (UT) befindet, und dem verbleibenden Brennraumvolumen, wenn sich der Kolben im oberen Totpunkt (OT) befindet.
Mathematisch lässt es sich als das Verhältnis aus der Summe von Hubvolumen und Brennraumvolumen zum Brennraumvolumen ausdrücken. Das bedeutet: Je größer das Hubvolumen im Vergleich zum Brennraumvolumen ist, desto höher ist das Verdichtungsverhältnis.
Ein höheres Verdichtungsverhältnis führt grundsätzlich zu einem besseren thermischen Wirkungsgrad, da die Temperatur- und Drucksteigerung während der Kompression effizienter genutzt wird. Allerdings sind hohe Verdichtungsverhältnisse insbesondere bei Ottomotoren durch die Klopfneigung begrenzt, da zu hohe Drücke und Temperaturen unkontrollierte Selbstzündungen auslösen können.
Steuerbarkeit des Kurbelwellenmotors (Variables Verdichtungsverhältnis)
Das variable Verdichtungsverhältnis (VCR – Variable Compression Ratio) ermöglicht es, das Verdichtungsverhältnis eines Motors während des Betriebs anzupassen. Es gibt Verbrennungsmotoren mit Kurbelwellenantrieb, bei denen eine flexible Steuerung des Druckbereichs möglich ist. Dies wird erreicht durch variable Ventilsteuerung, variable Verdichtung oder eine variable Turboladersteuerung. Am wirkungsvollsten ist jedoch die variable Verdichtungssteuerung. Diese Technologie ermöglicht eine präzise Anpassung des Verdichtungsverhältnisses und optimiert sowohl Effizienz als auch Leistung.
Allerdings ist die variable Verdichtungssteuerung immer mit mechanischen und aufwendigen Veränderungen der Motorgeometrie verbunden, was sich negativ auf Verschleiß und Haltbarkeit auswirken kann. Dennoch bietet diese Technologie eine außergewöhnliche Flexibilität, um einen Motor auf unterschiedliche Anforderungen hin zu optimieren, was insbesondere bei modernen Downsizing-Motoren von großer Bedeutung ist. Diese Motoren, mit kleineren Zylindervolumina und hohem Ladedruck, profitieren von der variablen Verdichtung besonders stark.
Die geometrische Veränderung des Motors zur Realisierung einer variablen Verdichtung ist komplex und anfällig, liefert jedoch beeindruckende Ergebnisse. Letztlich bleibt es eine Abwägung zwischen technischer Komplexität, Kosten und Nutzen – und die Entscheidung, welche Lösung die geeignetste ist, hängt von den spezifischen Anforderungen des Einsatzbereichs ab.
Geometrisches Verdichtungsverhältnis (Rotationskolbenmotor)
Beim Rotationskolbenmotor existiert genau wie bei einem Kurbelwellenmotor ein festes geometrisches Verdichtungsverhältnis. Dieses geometrische Verdichtungsverhältnis lässt sich sehr einfach über die Winkelbeziehung berechnen.
Ein Winkelwert ist aufgrund der geometrischen Funktionsbedingungen unveränderbar bzw. konstant. Das ist der maximale geometrische Hubwinkel HWkonst. Dieser geometrische Hubwinkel umfasst immer genau 61,88°, egal wie groß der Radius des Torus-Zylinders oder der Durchmesser der Kolben gewählt wird. Der maximale geometrische Kolbenwinkel KWmax errechnet sich dann aus (90° - HWkonst) / 2. Dieser maximale Wert 14,06° darf niemals vergrößert werden, da sich sonst die Kolben der beiden Steuerscheiben berühren würden.
Bild 9 zeigt die geometrischen Zusammenhänge, die das geometrische Verdichtungsverhältnis bestimmen.
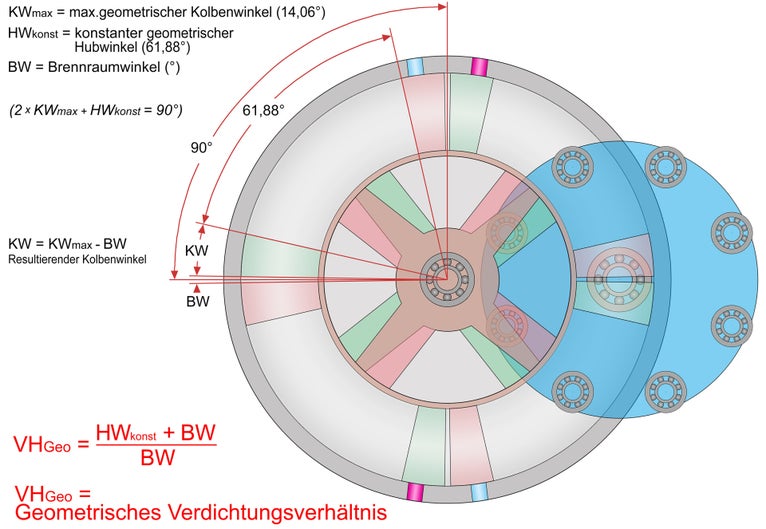
Verkleinern hingegen ist möglich, und diese Möglichkeit formt den Verbrennungsraum. Der daraus resultierende Brennraumwinkel BW liegt zwischen 2° und 4° und formt zunächst ein hohes Verdichtungsverhältnis. Die Zündkerzen- und Einspritzdüsenvertiefungen verringern das geometrische Verdichtungsverhältnis nach unten. Des Weiteren können auch Mulden auf beiden Seiten im Kolbenboden, veränderte Kolbenformen und zusätzliche Architekturänderungen in der Zylinderwand das geometrische Verdichtungsverhältnis zusätzlich nach unten reduzieren.
Um jetzt eine Flexibilität für eine variable Verdichtungs- und Volumensteuerung zu realisieren, benötigt man nur ein steuerbares Ventil zwischen Ansaugtakt und Verdichtungstakt.
Mit der Festlegung des Brennraumwinkels und der Kolbenarchitektur konstruiert man zunächst ein hohes geometrisches Verdichtungsverhältnis. Einmal durch die Architektur des Torus-Zylinders und des Kolbendurchmessers vorgegeben, erhält man einen Kurzhuber- oder einen Langhubermotor. Sinnvoll ist die Konstruktion eines Langhubers. Dieses einmal festgelegte hohe geometrische Verdichtungsverhältnis würde aber grundsätzlich die meisten Kraftstoffe, die mit Luft vermischt sind, in die Selbstzündung zwingen oder zumindest das Klopfverhalten ansprechen, das beides motorzerstörend wirken würde. Setzt man aber jetzt ein steuerbares Ventil zwischen Ansaug- und Verdichtungstakt ein, kann man durch gezielte Ansteuerung dieses Verdichtungsventils in Echtzeit einen gewünschten Anteil des zu verdichtenden Gemisches zurückführen, hinter den aktiven Kolben und damit zurückführen in den Ansaugvorgang. Diese Steuerbarkeit des eingebundenen Ventils senkt unmittelbar über die Volumenanpassung das hohe geometrische Verdichtungsverhältnis auf ein gewünschtes effektives Verdichtungsverhältnis ab.
Zusätzlich wird das angesaugte und zurückgeführte Gemisch nochmals homogener aufbereitet.
Was bewirkt die Verdichtungs- und Volumenventilsteuerung
Motoren arbeiten in verschiedenen Lastbereichen - Leerlauf, Teillast und Volllast.
Leerlaufbetrieb:
Der Motor läuft, ohne dass eine nennenswerte Last anliegt. Dieser Betriebszustand ist nur bei einem stehenden Fahrzeug, wenn kein Gang eingelegt ist.
Teillastbetrieb:
Der Motor arbeitet mit reduzierter Leistung, da die Energiezufuhr gedrosselt wird. Dies ist die häufigste Betriebsart im Alltag, z.B. beim Fahren mit konstanter Geschwindigkeit oder im Stadtverkehr.
Volllastbetrieb:
Der Motor arbeitet mit maximaler Leistung und liefert das höchstmögliche Drehmoment bei gegebener Drehzahl. Diese Betriebsart tritt typischerweise bei voller Beschleunigung oder unter schweren Lastbedingungen auf.
Letztere beiden Betriebsarten bilden den eigentlichen Fahrbetrieb im Auto ab, bei den moderne Motoren unverzüglich reagieren müssen, unter den Bedingungen möglichst effizient zu arbeiten.
Hier spielt die Verdichtungs- und Volumenventilsteuerung eine entscheidende Rolle.
Durch das Verdichtungsventil wird ein gewünschter Teil der bereits durchmischten Verbrennungsgase in den Ansaugkanal zurückgeführt. Die verbleibende Menge dieser zurückgeführten Gase beeinflusst unmittelbar das optimale Verdichtungsverhältnis, das für eine effiziente Verbrennung erforderlich ist.
Im Teillastbetrieb, bei geringeren Gasvolumina, sinkt zwar das Verdichtungsverhältnis, doch diesem Effekt kann gezielt entgegengewirkt werden – entweder durch eine kontrollierte Abgasrückführung oder durch die Anpassung der Gemischbildung auf ein mageres Kraftstoff-Luft-Verhältnis.
Ein präzise abgestimmtes System stellt sicher, dass der Rotationskolbenmotor in allen Lastbereichen mit einem optimalen Wirkungsgrad arbeitet und somit sowohl Effizienz als auch Leistungsfähigkeit maximiert werden.
Sogar unter der Verwendung zweier unterschiedlicher Kraftstoffe, sind die Vorzüge dieser Ventiltechnik denkbar. Ein Motor, der gleichzeitig mit zwei unterschiedlichen Kraftstoffen betrieben wird, wird als Dual-Fuel-Motor bezeichnet. Diese Motoren nutzen typischerweise eine Kombination aus Diesel und Autogas (CNG oder LNG), wobei der Diesel als Zündkraftstoff dient und das Autogas als Hauptkraftstoff.
Beim Rotationskolbenmotor mit einer variablen Verdichtungs- und Volumenventilsteuerung kann der Teillastbetrieb ausschließlich mit Autogas als Hauptkraftstoff erfolgen. Da Autogas (LPG) eine sehr hohe Klopffestigkeit aufgrund seines hohen Oktanwerts aufweist, kann – abhängig von der Gemischbildung (mager oder fett) – ein passendes Verdichtungsverhältnis von 12:1 bis 14:1 oder sogar höher angesteuert werden.
Durch die präzise Steuerung der Verdichtung wird die Effizienz des Motors maßgeblich erhöht, da eine höhere Verbrennungstemperatur erzielt wird. Gleichzeitig führt dies zu einer Reduzierung der Emissionen, insbesondere bei einem mageren Gasgemisch.
Nach der Verdichtung mit hohem Verdichtungsverhältnis folgt der Verbrennungsvorgang. Aufgrund der spezifischen Motorarchitektur (extremer Langhuber) ist der Expansionsverlauf besonders ausgedehnt. Dadurch endet die Expansionsphase mit einem geringen Restdruck, was die Energieeffizienz steigert – ähnlich dem Atkinson- oder Miller-Prinzip.
Wird unvermittelt Volllastleistung gefordert, kann zusätzlich Diesel oder Benzin eingespritzt werden. Dies kann sowohl bei einem geringen variablen Verdichtungsverhältnis während der Verdichtungsphase (vor OT) als auch bei einem höheren Verdichtungsverhältnis während der Verbrennungsphase (nach OT) erfolgen, um eine optimale Leistungsentfaltung zu gewährleisten.
Die in Echtzeit ausgeführten Steuerungsmöglichkeiten des Verdichtungsventils ermöglichen eine Vielzahl von Lastzuständen, die im täglichen Fahrbetrieb direkt und mit voller Leistung abrufbar sind, wodurch eine außergewöhnliche Fahrdynamik und Effizienz gewährleistet werden.
Bild 10: Die transparente Darstellung zeigt den Ansaug- und Verdichtungsvorgang zwischen zwei Kolben einer Steuerscheibe. Über den Bypass (grün dargestellt) kann das Verdichtungsgemisch zurückgeführt werden.
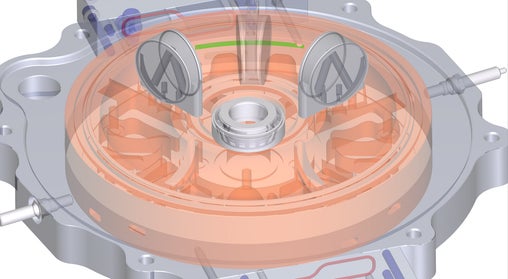
Bild 11: Die Funktionsdarstellung zeigt das Arbeitsprinzip des Verdichtungsventils, das sich im äußeren Bereich des Motors befindet und die verdichteten Treibstoffgase zurück in den Ansaugbereich führen kann.
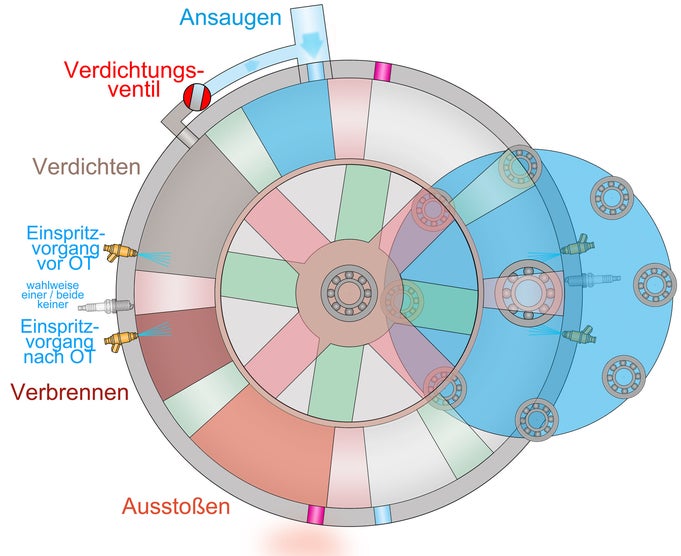
Thema 3: Thermische Eigenschaften
Thermische Verluste (allgemein)
Die thermischen Verluste sind der größte Faktor für den Energieverlust in Verbrennungsmotoren. Bei Motoren mit größeren Kolben-Zylinder-Paarungen sind diese Verluste jedoch tendenziell geringer. Das liegt daran, dass das Volumen eines Zylinders mit der dritten Potenz (kubisch) ansteigt, während die Oberfläche nur mit der zweiten Potenz (quadratisch) wächst. Dadurch wird das Verhältnis von Oberfläche zu Volumen (S/V-Verhältnis) günstiger, was die Wärmeverluste über die Zylinderwände verringert. Zusätzlich beeinflussen die geometrischen Eigenschaften des Motors die thermischen Verluste maßgeblich.
Das Langhuberprinzip – bei dem der Hub länger ist als der Kolbendurchmesser – bietet in diesem Zusammenhang klare Vorteile gegenüber dem Kurzhuberprinzip. Langhuber haben eine kleinere Kolbenfläche und einen längeren Zylinder. Das bedeutet, dass weniger Wärme über den Kolbenboden und den Zylinderkopf verloren geht, insbesondere in der kritischen Anfangsphase der Verbrennung, in der die Wärmeverluste am größten sind. Diese geometrische Konfiguration ermöglicht eine effektivere Energieübertragung während der Expansion und trägt zur Reduzierung der Wärmeverluste bei.
Ein weiterer Vorteil des Langhubers liegt in der längeren Expansionsphase. Während der
Expansion dehnen sich die Verbrennungsgase aus, kühlen dabei ab und verlieren an Druck.
Dieser Prozess kann – unter idealen Bedingungen – annähernd adiabatisch ablaufen. Das bedeutet, dass kaum Wärme an die Umgebung abgegeben wird, sondern die gesamte Energie der Gase zur Arbeit am Kolben genutzt wird. Je länger die Expansion dauert, desto mehr Arbeit kann aus den Verbrennungsgasen gewonnen werden, bevor der Druck zu gering wird. Besonders bei einem Langhuber, der eine längere Strecke für die Expansion bietet, geschieht diese Abkühlung der Gase unter einem höheren Druckniveau. Das hält den thermischen Wirkungsgrad während der Expansion auf einem vergleichsweise hohen Niveau.
Der Kolben und seine Aufgabe
Der Kolben im Verbrennungsmotor ist eine Schlüsselkomponente, die maßgeblich die Leistung, Effizienz und Langlebigkeit des Motors beeinflusst. Er wandelt die Verbrennungsenergie in mechanische Arbeit um und spielt eine zentrale Rolle bei der Wärmeübertragung und den Bewegungsprozessen. Durch die extremen Temperaturen und Drücke im Motor muss der Kolben präzise arbeiten und gleichzeitig mechanische Belastungen und Wärme managen.
Um dauerhafte Effizienz zu gewährleisten, ist eine ausreichende Kühlung des Kolbens entscheidend. Zu hohe Temperaturen können den Kolben verformen oder zu Klopfen führen, was die Verbrennung beeinträchtigt und Schäden verursacht. Zudem kann übermäßige Wärme die mechanischen Eigenschaften des Materials, wie Festigkeit und Härte, negativ beeinflussen.
Während die notwendige Kühlung einen Teil der Verbrennungswärme abführt und somit die thermische Effizienz des Motors verringert, ist sie unerlässlich, um diese genannten Probleme zu verhindern. Moderne Motoren suchen nach einem optimalen Kompromiss, den Kühlpunkt möglichst so zu wählen, dass die Stabilität hoch und die thermischen Verluste gering bleiben.
Der Rotationskolbenmotor
Neben den Vorteilen des verbauten Langhuberprinzips und des Verdichtungsventils gibt es jedoch noch weitere Vorteile dieser neuen Technik. Alle acht Kolben durchlaufen nur einen Kreiszylinder (Torus-Zylinder) und verrichten dabei 8 Doppelarbeitstakte, also 16 Verbrennungsabläufe pro Umdrehung. Jeder Kolben übernimmt immer gleichzeitig zwei Arbeitstakte. 2x Ansaugen und Verdichten, 2x Verdichten und Verbrennen, 2x Verbrennen und Ausstoßen und 2x Ausstoßen und Ansaugen. Der dadurch resultierende geringere Temperaturgradient verringert gleichzeitig die thermischen Verluste, da durch die vorgegebene Architektur alle notwendigen Abläufe schneller durchlaufen werden.
Das Besondere: Die Kolben des Rotationskolbenmotors
Die acht Kolben des Rotationskolbenmotors sind komplett anders konstruiert als herkömmliche Kolben, die über das bewegliche Pleuel ihre Energie weiterleiten. Jeder einzelne Kolben ist seitlich in einer Kreiszylinderhälfte verschraubt und bildet damit eine feste Einheit mit der Steuerscheibe. Durch diese gewählte Konstruktion eröffnet sich eine perfekte technische Möglichkeit, die Kolben von innen mit einer Flüssigkühlung zu kombinieren.
Je nach Leistungsforderung kann diese Kolbenkühlung auch geregelt werden. Verformungen und Klopfneigung werden damit ausgeschlossen. Da diese Regelung sehr präzise abläuft, kann man den symmetrisch gebauten Kolben auf beiden Seiten mit einer Platte verschließen, die die Eigenschaft einer niedrigen Wärmeleitfähigkeit aufzeigt. Das Grundgerüst des Kolbens besteht aus hochfestem Aluminium, ähnlich wie bei allen bekannten Kolben im Motorenbau.
Aluminium hat die Eigenschaft einer sehr hohen Wärmeleitfähigkeit. Diese Eigenschaft ist für den thermischen Expansionsverlauf aber sehr nachteilig und mindert den Wirkungsgrad. Mit dem vollflächigen Abschluss beider Kolbenseiten mit beispielsweise Edelstahl mindert sich erheblich die Wärmeleitfähigkeit an diesen kritischen Punkten.
Bild 12: Die Darstellung zeigt vier Kolben einer Steuerscheibe mit Öl-Kühlungskreislauf und thermischen Abschlussdeckeln auf beiden Seiten der Kolbenkonstruktion
(Abbildung aus bereits optimierten Konzept)
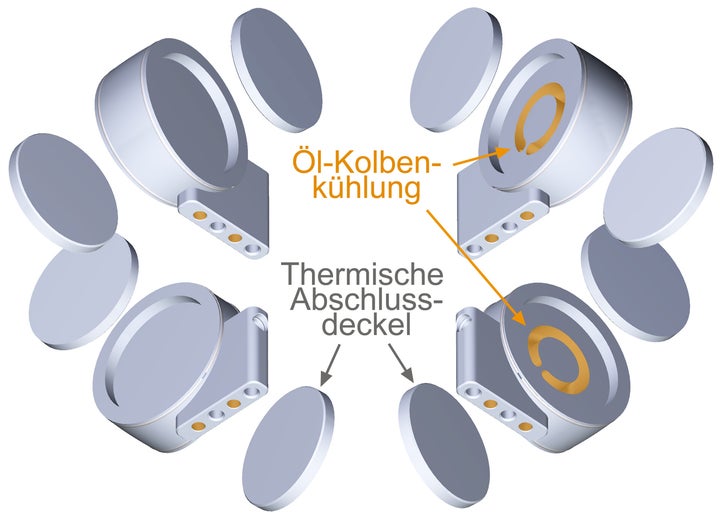
Zu Beginn der Verbrennungsphase stehen sich immer zwei Kolben unmittelbar gegenüber. Der Verbrennungsprozess kann deutlich verlustfreier beginnen, da die Fläche die die Verbrennungsgase umschließen, hauptsächlich durch die Kolbenflächen aus Edelstahl bestimmt wird. Erst später wird der Anteil der Fläche durch die freiwerdende Zylinderwand größer.
Die Wärmeleitfähigkeit von Aluminium liegt bei ca. 205W/mK, die Wärmeleitfähigkeit von Edelstahl liegt bei ca. 16W/mK.
Da es keine empfindlichen Bauteile wie Zylinderkopf, Zylinderkopfdichtung und Ventile mit Ventilpassungen in diesem geschlossenen und verdichteten Expansionsraum gibt und die Kolbenringe ausreichend Kühlung über den Ölkreislauf des Kolbens erhalten, ist die Gefahr das über die
deutlich hohen Temperaturen Schäden entstehen, sehr gering.
Sogar die Zündkerze, die nur für einen sehr kurzen Moment ihre Aufgabe erfüllt, das Gemisch zu entzünden, verbleibt lediglich für einen Augenblick im verdichteten Brennraum. Unmittelbar nach der Zündung wird sie von einer Kolbenflanke verdeckt.
Wenn jetzt neben den Kolbenköpfen auch die Lauffläche der Zylinderwand aus einem Material mit geringerer Wärmeleitfähigkeit ausgeführt ist, kann in der Expansionsphase nur noch geringe Menge an Wärmeenergie verloren gehen. Das beschriebene Zusammenspiel bewirkt eine Stabilisierung der unteren Arbeitstemperatur und verringert den Temperaturgradienten innerhalb der wenigen Bauteile. Der Expansionsprozess in dieser temperaturstabilisierten Langhuberarchitektur ermöglicht damit einen gezielten Verbrennungsprozess mit großer Temperaturspanne für eine effiziente Umsetzung in mechanische Energie. Ein annähernd idealer adiabatischer Expansionsverlauf wird dabei unterstützt, da die geringe Wärmeabgabe die Temperaturdifferenz während der Expansion minimiert und eine nahezu isentrope Ausdehnung fördert. Dies maximiert den Druckaufbau und optimiert den Übergang der thermischen Energie in mechanische Arbeit, was die Effizienz weiter steigert und gleichzeitig den Kraftstoffverbrauch reduziert.
Kurbelwelle vs. neuartige Kulissenwelle
Der Bewegungsablauf der Kolben im Kurbelwellenmotor und im Rotationskolbenmotor wird durch die unterschiedliche Geometrie des Antriebsmechanismus bestimmt und beeinflusst direkt den Verlauf von Kolbenweg, Kolbengeschwindigkeit und Kolbenbeschleunigung. In den folgenden ersten drei Funktionsdarstellungen werden die zwei unterschiedlichen kinematischen Konzepte analysiert, die jeweils einen Kolben von OT nach UT in der Expansionsphase bewegen. Während der gesamte Hubweg in Bild 13 ausschließlich von der Winkelstellung der Abtriebswelle abhängt, kommt in den Darstellungen von Bild 14 und Bild 15 zusätzlich der zeitliche Verlauf ins Spiel. Da Drehzahländerungen einen maßgeblichen Einfluss auf Geschwindigkeit und Beschleunigung haben, konzentriert sich der folgende Vergleich ausschließlich auf die Charakteristik der Bewegungsabläufe.
In Bild 16 wird dann der umgekehrte Verlauf, die Verdichtungsphase, analysiert.
Bild 15 und Bild 16 zeigen auch die typisch kritischen bis unkritischen Bereiche der Expansion und der Verdichtung auf.
Expansionsphase (nach Verbrennung von OT nach UT)
Ein konstanter Kolbenbeschleunigungsverlauf in der ersten Hälfte von OT nach UT kann eine gleichmäßigere Druckverwertung unterstützen, insbesondere während der kritischen Hochdruckphase der Verbrennung (siehe Bild 15). Da die Expansion in diesem Bereich am stärksten ist, beeinflusst die Kolbenbewegung direkt die Volumenvergrößerung und damit den Druckverlauf. Eine zu früh abnehmende Beschleunigung führt zu einer ungleichmäßigen Expansion, wodurch Druckspitzen nicht optimal genutzt werden und Verluste durch Wärmeübertragung an die Zylinderwand steigen können. Ein gezielter Beschleunigungsverlauf kann somit die Umsetzung des adiabatischen Ideals verbessern, indem er eine kontrollierte und effiziente Energieübertragung in mechanische Arbeit ermöglicht.
Verdichtungsphase (von UT nach OT)
Während der Verdichtung, insbesondere im kritischen oberen Bereich kurz vor dem oberen Totpunkt (OT), sollte die Beschleunigung negativ sein, d.h. die Beschleunigung des Kolbens nimmt ab, je näher er dem OT kommt (sieh Bild 16). Diese negative Beschleunigung ist vorteilhaft, da sie den Kolben langsamer macht, wenn der Druck im Zylinder am höchsten ist.
Eine gleichmäßige Verringerung der Beschleunigung sorgt für einen kontrollierten und gleichmäßigen Kompressionsprozess, wodurch die Erhöhung des Drucks langsamer und stabiler erfolgt. Eine gleichmäßige, negative Beschleunigung kann dabei helfen, eine Überhitzung und unerwünschte Frühzündungen zu vermeiden, was besonders im kritischen oberen Bereich der Verdichtung von Bedeutung ist. Hinzu kommt, dass das gewünschte Verdichtungsverhältnis etwas höher angesetzt werden kann, da der Druckaufbau in der kritischen Verdichtungsphase langsamer verläuft, was zu einer besseren thermischen Kontrolle führt und eine effizientere Verdichtung ermöglicht.
Die Grafik in Bild 13 zeigt den charakteristischen Kolbenweg von OT nach UT in der Expansionsphase.
Die rote Linie stellt
den Verlauf des Rotationskolbenmotors
dar, die blaue Linie
stellt den Verlauf des Kurbelwellenmotors
dar.
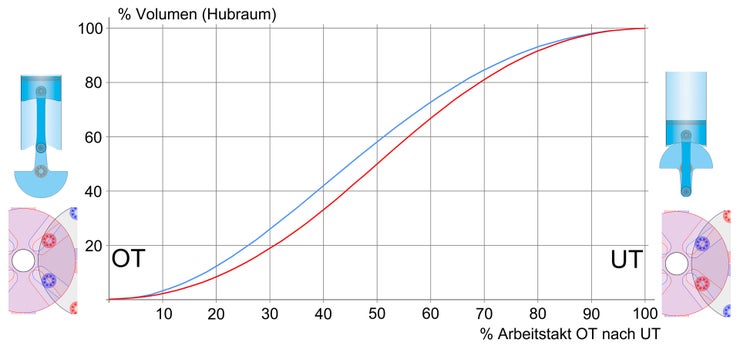
Die Grafik in Bild 14 zeigt die charakteristische Kolbengeschwindigkeit von OT nach UT in der Expansionsphase. Die rote Linie stellt den Verlauf des Rotationskolbenmotors dar, die blaue Linie stellt den Verlauf des Kurbelwellenmotors dar.
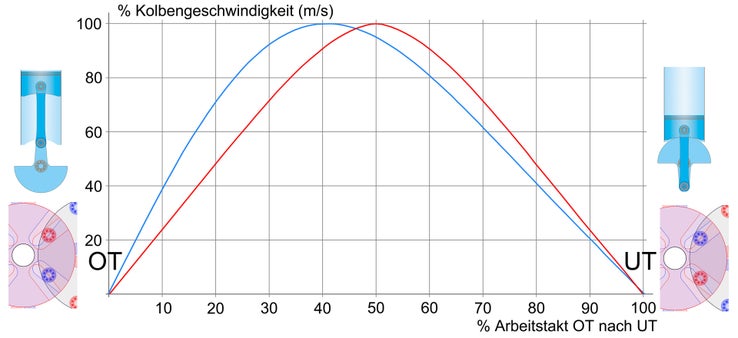
Die Grafik in Bild 15 zeigt die charakteristische Kolbenbeschleunigung von OT nach UT in der Expansionsphase. Die rote Linie stellt den Verlauf des Rotationskolbenmotors dar, die blaue Linie stellt den Verlauf des Kurbelwellenmotors dar.
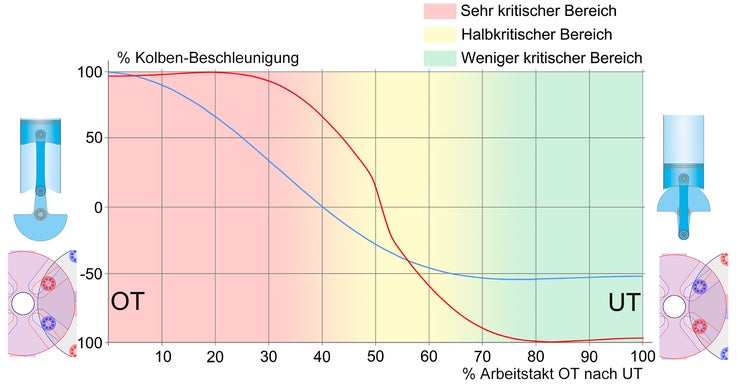
Die Grafik in Bild 16 zeigt die charakteristische Kolbenbeschleunigung von UT nach OT in der Verdichtungsphase. Die rote Linie stellt den Verlauf des Rotationskolbenmotors dar, die blaue Linie stellt den Verlauf des Kurbelwellenmotors dar.

Fazit:
In der vorliegenden Analyse wurde der Verdichtungs- und Expansionsprozess der beiden Systeme mit unterschiedlichen Geometrien verglichen. Insbesondere die Bedeutung der gleichmäßigen Beschleunigung unter Einbezug der kritischen Bereiche, sowohl bei der Verdichtung als auch bei der Expansion, wurde herausgestellt.
Verglichen mit der Kurbelwelle, die ein eher ungleichmäßiges oder weniger kontrolliertes Beschleunigungsprofil aufweist, erfüllt die neuartige Kulissenwelle diese Anforderungen deutlich besser. Durch ihre Konstruktion ermöglicht sie eine gleichmäßigere Verdichtung und Expansion, wodurch thermische Verluste minimiert und die Effizienz des Motors optimiert wird.
Zusammenfassend lässt sich sagen, dass die neuartige Kulissenwelle mit ihrem optimalen Beschleunigungsprofil besser in der Lage ist, die thermodynamischen Anforderungen der Verbrennung und der Verdichtung effizient zu erfüllen.
Thema 4: Leistungen und Dimensionen
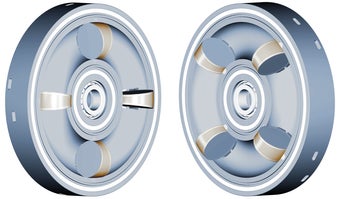
vs.
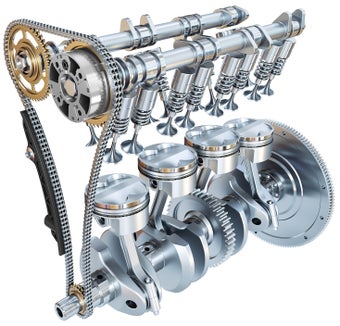
Ein 4-Takt-Verbrennungsmotor mit Kurbelwellenantrieb erzeugt pro Zylinder alle 720° Kurbelwellenumdrehung einen Arbeitstakt. In einem 4-Zylinder-Motor entstehen somit alle 360° zwei Arbeitstakte. Sobald ein Arbeitstakt eines Zylinders endet, beginnt der nächste eines zweiten Zylinders. Der Motor besteht aus vier Kolben, vier Zylindern und einer Kurbelwelle mit 4 Pleuelstangen.
Der Rotationskolbenmotor, bestehend aus zwei Steuerscheiben die jeweils eine Einheit aus 4 Kolben und einer Kreiszylinderhälfte kombinieren, hat alle 360° Umdrehung an der Abtriebswelle 8 Doppel-Arbeitstakte, das bedeutet, das immer 2 sich gegenüberliegende und damit symmetrische Arbeitstakte gleichzeitig erfolgen.
Alle acht Kolben durchlaufen somit nur einen Kreiszylinder (Torus-Zylinder) und verrichten dabei 16 Verbrennungsabläufe pro Umdrehung. Jeder Kolben übernimmt immer gleichzeitig zwei Arbeitstakte. 2x Ansaugen und Verdichten, 2x Verdichten und Verbrennen, 2x Verbrennen und Ausstoßen und 2x Ausstoßen und Ansaugen.
Die Darstellung in Bild 17 zeigt die Arbeitstakte, die jeder Kolben bei einer 360° Umdrehung vollzieht.
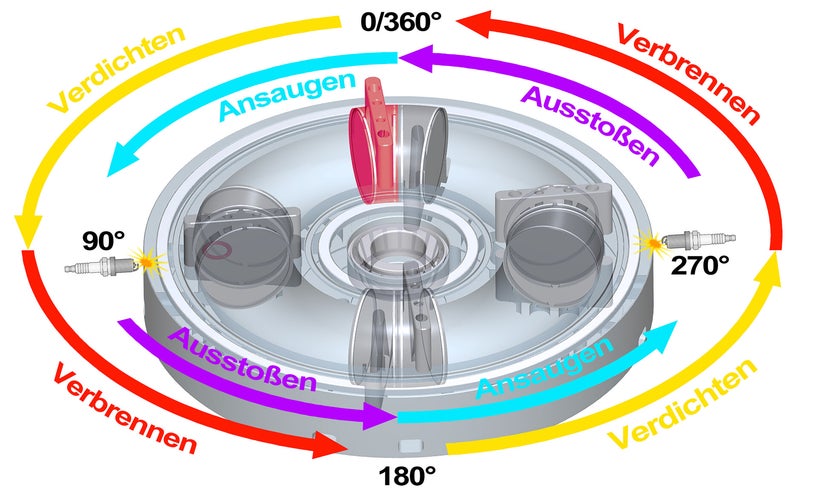
Was unterscheidet den Kurbelwellenmotor vom Rotationskolbenmotor in ihrem Arbeitsablauf und ihrer Leistungscharakteristik
Da der 4-Zylinder-Kurbelwellenmotor pro Umdrehung lediglich zwei Arbeitstakte an die Abtriebswelle abgibt, muss der Spitzendrehmomentwert mehr als doppelt so hoch ausfallen, um die Leistungsanforderungen zu erfüllen. Im Gegensatz dazu verteilt sich die Kraftentfaltung bei einem Rotationskolbenmotor auf acht Doppelarbeitstakte, die jeweils in einer symmetrischen 180°-Anordnung ablaufen. Dies reduziert die Spitzenbelastung der Bauteile, ermöglicht eine kompaktere Bauweise und senkt das Gewicht, ohne die Leistungsfähigkeit zu beeinträchtigen.
Die Grafik in Bild 18 vergleicht den charakteristischen Drehmomentverlauf an der Abtriebswelle eines Rotationskolbenmotors mit einem
4-Zylinder Kurbelwellenmotor. Die Leistung bei gleicher Drehzahl ist ungefähr
identisch.
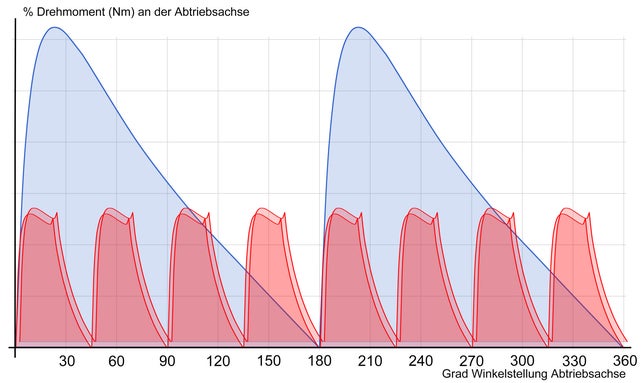
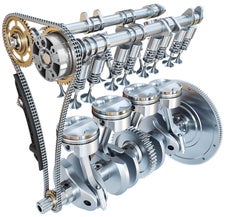
vs.
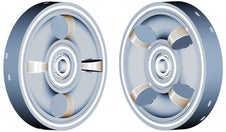
Beim 8-Zylinder-Kurbelwellenmotor entstehen 4 Arbeitstakte pro 360°-Umdrehung an der Kurbelwelle. Das sorgt für eine deutliche Reduzierung der Drehmomentspitzen und verbessert die Laufruhe. Allerdings geht diese Bauweise mit einem hohen konstruktiven Aufwand einher.
Für eine vollständige Umdrehung der Kurbelwelle sind 16 reziproke Kolben- und Pleuelbewegungen erforderlich, was nicht nur zu erhöhten Massenkräften, sondern auch zu einer komplexeren Lagerung und Schmierung führt. Zudem erfordert die Ventilsteuerung eine Vielzahl an Bauteilen, darunter doppelte Nockenwellen oder eine aufwendige Kipphebelmechanik. Der höhere Materialeinsatz, die aufwendigere Fertigung und der größere Platzbedarf machen den 8-Zylinder-Motor schwerer, teurer und komplizierter in der Wartung als kleinere Motorenkonzepte.
Die Grafik in Bild 19 vergleicht den charakteristischen Drehmomentverlauf an der Abtriebswelle eines Rotationskolben-motors mit einem 8-Zylinder Kurbelwellenmotor. Die Leistung bei gleicher Drehzahl ist ungefähr
identisch.
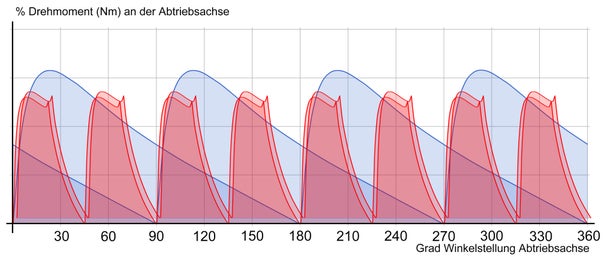
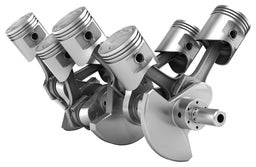
vs.
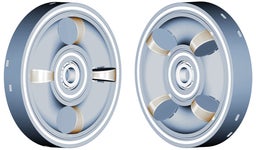
Thema 5: Energieeffizienz und Flexibilität
Wie bereits im Vorfeld dargestellt, arbeiten beide Motorsysteme mit Kolben und Zylindern, um chemische Energie in mechanische Energie umzuwandeln. Der wesentliche Unterschied liegt in den spezifischen geometrischen Zwangsführungen (klassische Kurbelwelle und neuartige Kulissenwelle), die den Bewegungsablauf der Kolben innerhalb der Zylinder bestimmen. Diese kinematischen Vorgaben beeinflussen nicht nur die Annäherung an ideale Verbrennungsprozesse, sondern auch die thermodynamische Effizienz. Darüber hinaus ermöglichen sie eine differenzierte Anpassung der Leistungsabgabe, indem sie variable Betriebsparameter wie Verdichtungsverhältnis, Füllungsgrad und Verbrennungsgeschwindigkeit steuern. Diese Faktoren sind entscheidend, um eine hohe Effizienz mit optimierter Leistungsentfaltung zu verbinden.
Die Geometrie der Kurbelwelle in einem typischen Automobil-Verbrennungsmotor wird maßgeblich durch die vorhandenen Bauraumvorgaben bestimmt. Eine kompakte Bauweise muss dabei mit der erforderlichen Flexibilität für eine präzise Leistungsanpassung kombiniert werden. Das Kurzhuberprinzip erfüllt diese Anforderungen, indem es eine hohe Drehfreudigkeit bei geringen Baumaßen und Gewichten vereint und damit ideale Voraussetzungen für moderne Fahrzeuge schafft.
Allerdings geht diese kompakte Bauweise mit Nachteilen einher: Die Vorteile eines Langhubmotors – insbesondere die thermodynamisch effizientere Verbrennung – bleiben ungenutzt. Während Langhuber eine bessere Energieausnutzung ermöglichen, erfordern sie gleichzeitig größere Baumaße und ein höheres Gewicht, was ihre Integration in moderne Fahrzeugkonzepte erschwert.
Eine ideale Kombination aus den Effizienzvorteilen des Langhubers und der platzsparenden, drehfreudigen Bauweise des Kurzhubers wäre wünschenswert. In der Praxis stößt eine solche Lösung jedoch an konstruktive und thermodynamische Grenzen, weshalb meist ein Kompromiss zwischen Kompaktheit, Effizienz und Leistungsfähigkeit erforderlich ist.
Die beiden nachfolgenden Grafiken verdeutlichen, dass die geometrischen Vorgaben der einzelnen Kolben-Zylinder-Kombinationen stets voll ausgeschöpft werden müssen. Der Kolben bewegt sich zwangsgeführt über die gesamte Zylinderlänge in einer linearen Auf- und Abwärtsbewegung, wodurch kaum Spielraum für Flexibilität bleibt. Zudem setzen die festen kinematischen Abläufe klare Grenzen, sodass die Bewegungsdynamik nicht ideal an den Verbrennungsprozess angepasst werden kann. Dies führt zu einem unvermeidbaren Kompromiss innerhalb eines starren technologischen Rahmens.
Verdichtungsphase
Kurbelwellenmotor
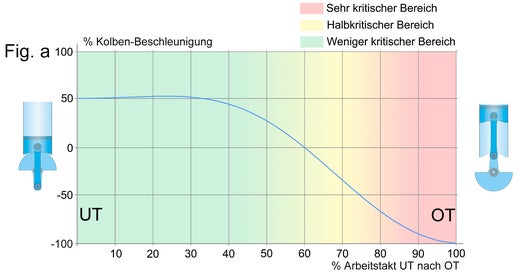
Expansionsphase
Kurbelwellenmotor
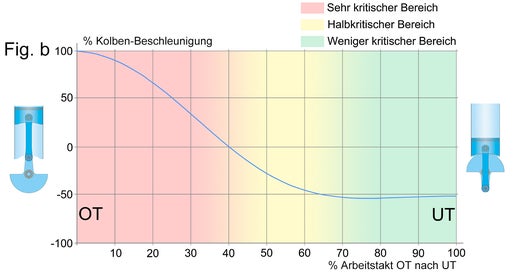
Die Grafik in Bild 20 veranschaulicht die charakteristische Kolbenbeschleunigung eines Kurbelwellenmotors in der Verdichtungsphase (links, Fig. a) von UT nach OT sowie in der Expansionsphase (rechts, Fig. b) von OT nach UT.
Bei diesem klassischen Kurzhuber wird das gesamte Arbeitsvolumen vollständig genutzt. Dabei durchläuft die Kolbenbeschleunigung die kritischen Bereiche (von rot bis gelb bzw. von gelb bis rot) mit einem nicht idealen Beschleunigungsverlauf.
Der Rotationskolbenmotor mit seiner neuartigen Kulissenwelle ist durch seinen endlos Torus-Zylinder flexibler in der Nutzung der Umsetzung von Verbrennungsenergie in mechanische Energie. Zwar durchlaufen die Kolben auch ein fest vorgegebenes geometrisches Funktionsschema, aber die Gestaltung, ob Langhuber oder Kurzhuber haben keine maßgeblichen Konsequenzen auf Bauraum und Drehfreudigkeit. Die steuerbare und damit anpassungsfähige Gestaltung des Arbeitsvolumens, wie es die nachfolgenden Grafiken deutlich machen, kann zwischen effizientem Teillastbetrieb oder leistungsstarkem Volllastbetrieb variieren. Die idealisierte Kolbenbewegung sowohl in der Verdichtungsphase als auch in der Expansionsphase, verbunden mit verbesserten thermischen Bedingungen über eine aktive Kolbenkühlung, als auch die Tatsache, der geringen Anteile verwendeter Bauteile machen den Rotationskolbenmotor zu einem starken Konkurrenten als Motor für den Antrieb in Fahrzeugen. Darüber hinaus überzeugt die kleinere Baugröße und das geringe Gewicht.
Verdichtungsphase
Rotationskolbenmotor
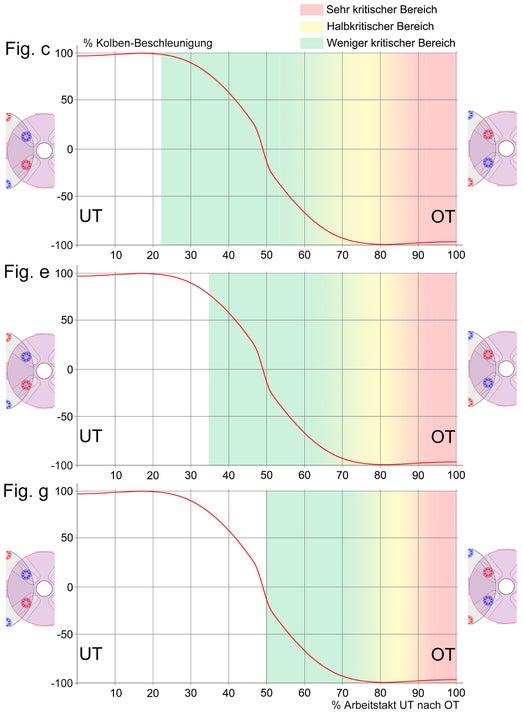
Expansionsphase
Rotationskolbenmotor
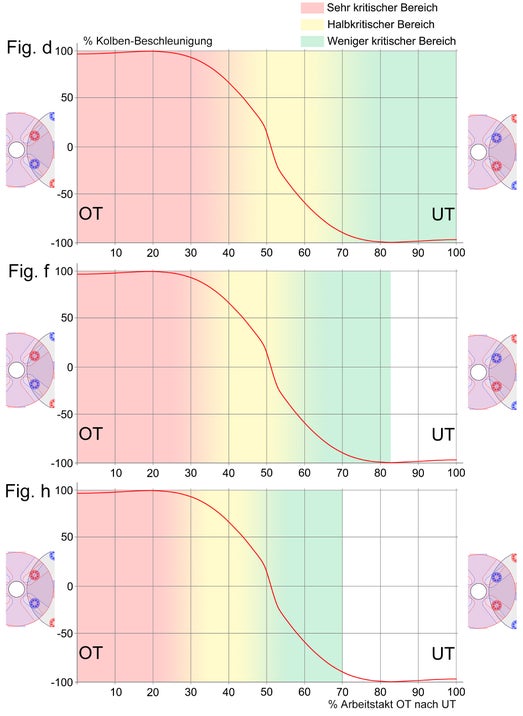
Die Grafik in Bild 21 veranschaulicht die charakteristische Kolbenbeschleunigung eines Rotationskolbenmotors in der Verdichtungsphase (links, Fig. c, e und g) von UT nach OT sowie in der Expansionsphase (rechts, Fig. d, f und h) von OT nach UT. Zur Darstellung der steuerbaren Arbeitsvolumina sind drei Beispiele aufgeführt. Besonders in den kritischen Bereichen (von rot bis gelb, bzw. von gelb bis rot) wird der ideale, gleichmäßige Beschleunigungsverlauf des Kolbens sichtbar.
Dabei gilt: Je kleiner das gewählte Volumen, desto optimaler gestaltet sich dieser Beschleunigungsverlauf.
Thema 6: Kinematische und dynamische Unterschiede
In technischen Anwendungen werden Massen oft oszillierend bewegt – entweder linear entlang einer geraden Linie oder rotierend um eine Achse. Beide Systeme weisen gemeinsam auf, dass die Massen während ihres Bewegungszyklus für einen kurzen Moment vollständig zum Stillstand kommen, bevor sie erneut beschleunigt werden. Trotz dieser Gemeinsamkeit bleibt der Energiebedarf und der Verschleiß rotierender symmetrischer Massen geringer als bei linearen Massen, was auf grundlegende mechanische und dynamische Unterschiede zurückzuführen ist.
Bei diesem Vergleich ergeben sich kinematische und dynamische Unterschiede:
1. Rotierende symmetrische Massen (Rotationskolbenmotor)
Die Bewegung der Steuerscheiben mit Kolben beim Rotationskolbenmotor erfolgt entlang einer Kreisbahn um eine zentrale Achse. Während des oszillierenden Drehmoments wird die Winkelgeschwindigkeit kontinuierlich erhöht oder reduziert, wobei die Masse am Umkehrpunkt vollständig abgebremst wird. Die Kräfte wirken gleichmäßig verteilt um die Drehachse, da die Masse symmetrisch konstruiert ist. Dies führt zu einer gleichmäßigen Verteilung von Trägheitskräften und minimiert ungewollte Schwingungen.
2. Linear hin- und herbewegte Massen (Kurbelwellenmotor)
Die Kolben- und Pleuelbewegung beim Kurbelwellenmotor erfolgt entlang einer Linie, wobei die Geschwindigkeit ebenfalls bei jedem Zyklus vollständig auf Null reduziert wird. Anschließend wird die Masse in die entgegengesetzte Richtung beschleunigt. Im Gegensatz zu rotierenden Massen tritt hier ein kompletter Richtungswechsel der Bewegung auf, was zusätzliche mechanische Belastungen verursacht.
Energiebedarf und Verluste
1. Kinetische Energie
Für beide Systeme ist die kinetische Energie proportional zur Masse und zur Geschwindigkeit.
Während die benötigte Energie für das Beschleunigen und Abbremsen theoretisch gleich groß ist, entstehen bei linearen Massen zusätzliche Verluste, da die Richtungsumkehr im linearen System die Trägheitskräfte vollständig in entgegengesetzter Richtung aufbaut. Dies erfordert zusätzliche Energie und erhöht die Belastung der Führungen. Die mechanische Reibung ist entlang der Führungen (Zylinder) typischerweise größer als bei rotierenden Lagern, da die Kontaktfläche oft weniger gleichmäßig ist. Die Geometrie eines Kurbelwellenmotors erfordert mehr Reibung von Kolben und Zylinder durch schräg einwirkende Kräfte basierend auf die Pleuelwinkelstellungen. Lineare Systeme erzeugen mehr Schwingungen und Vibrationen, die wiederum mehr Energie dissipieren als symmetrisch rotierende Massen.
2. Mechanische Belastung
Symmetrisch konstruierte rotierende Systeme verteilen die Kräfte gleichmäßig um die Achse, wodurch geringere Spitzenlasten auftreten. Dies reduziert Energieverluste durch Reibung und Schwingungen. Bei der Umkehrung der Bewegungsrichtung in linearen Systemen treten zusätzliche Belastungen durch Stoß- und Vibrationseffekte auf. Diese Belastungen können Energieverluste erhöhen und den Verschleiß mechanischer Komponenten beschleunigen.
3. Energieeffizienz
Wenn beide Systeme denselben Bewegungszyklus mit identischer Beschleunigung, Verzögerung und Masse durchlaufen, können rotierende symmetrische Massen dennoch bis 30 % weniger Energie benötigen. Die entscheidenden Faktoren sind:
- Die Vermeidung der vollständigen Umkehrung der Bewegungsrichtung bei rotierenden Massen.
- Gleichmäßig verteilte Kräfte, die Reibungsverluste und Vibrationen reduzieren.
- Die geringere mechanische Belastung der Komponenten, was die Verluste zusätzlich minimiert.
Auch wenn sich beide Systeme im Stillstandmoment gleichen, bleibt der Vorteil rotierender symmetrischer Massen aufgrund ihrer gleichmäßigen Kräfteverteilung und des Wegfalls der Richtungsumkehr bestehen. Die Energieverluste sind geringer, da Trägheitskräfte effizienter gehandhabt werden können und mechanische Belastungen reduziert sind. In Verbrennungsmotoren, bei denen oszillierende Bewegungen erforderlich sind, stellen rotierende symmetrische Massen daher eine energetisch günstigere Lösung dar.
Symmetrisches Kräftegleichgewicht mit dynamischer Energieübertragung
In der Geometrie des Rotationskolbenmotors laufen immer zwei Steuerscheiben mit 4 Kolben in dieselbe Drehrichtung in einem reziproken Bewegungsablauf. Jeder Scheibe wird von Null aus beschleunigt bis zu ihrer maximalen Geschwindigkeit und dann im umgekehrten Verlauf wieder abgebremst. Dieser Bewegungsablauf pro Scheibe beträgt genau 90°. Die sich schneller bewegende Scheibe ist die aktive Steuerscheibe, während die sich langsamer bewegende Scheibe die Aufgabe der passiven Steuerscheibe übernimmt. Die Bewegungsprozesse der einzelnen Scheiben überschneiden sich jeweils bei 45° und ihre Arbeitsaufgaben wechseln sich. In diesem wechselnden Bewegungsbereich sind die Geschwindigkeiten annähernd gleich groß, aber sie sind gegenläufig. In diesem mittleren Geschwindigkeitsbereich heben sich die Kräfte annähernd auf (siehe hierzu Figur a), während jede Scheibe genau zwischen dem 45° Wechselpunkt eine Richtungsumkehr erfährt. Da die Geschwindigkeiten dieser Richtungsumkehr sehr unterschiedlich sind, entsteht ein sehr ungleichmäßiger Kräfteaustausch. Dieser ungleichmäßige Kräfteaustausch bewirkt Vibrationen und erhöht damit den Energieverlust.
Kombiniert man jetzt zwei gleiche Rotationskolbenmotoren mit einem Phasenversatz von 22,5° auf eine gemeinsame Abtriebswelle, dann heben sich in gleich drei Geschwindigkeitsebenen die Kräfte fast vollständig auf (siehe hierzu Figur b). Durch diese Kombination zweier Rotationskolbenmotoren mit insgesamt vier Steuerscheiben entsteht ein symmetrisches Kräftegleichgewicht mit einer dynamischen Energieübertragung. Die Vibrationen und damit auch der Energieverlust reduzieren sich annähernd gegen Null.
Die Grafik in Bild 22 zeigt den Geschwindigkeitsverlauf der Steuerscheibenpaare. Figur a zeigt ein Doppelscheibenpaar, Figur b zeigt zwei Doppelscheibenpaare mit einer Phasenverschiebung von 22,5°.
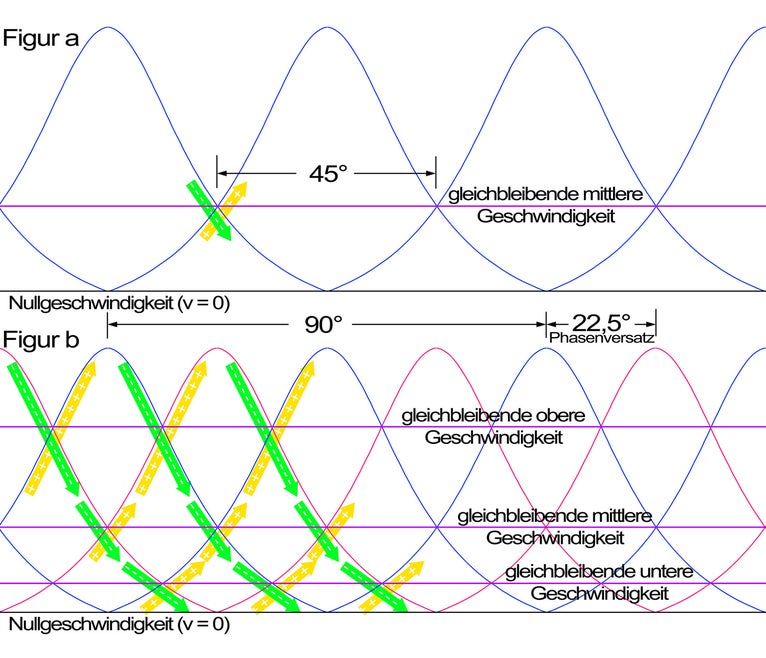
Die Grafik in Bild 23 zeigt einen charakteristischen Drehmomentverlauf an der Abtriebswelle eines doppelten Rotationskolben-motors. Insgesamt gibt es 16 Doppel-arbeitstakte pro Umdrehung..
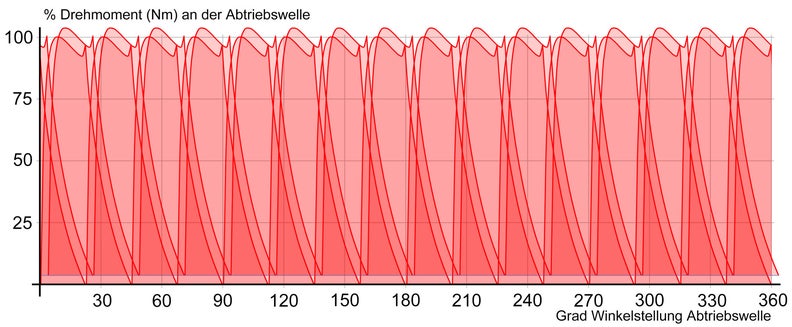
Thema 7: Optimierte Abdichtung im Rotationkolbenmotor
Hydrostatische und hydrodynamische Lösungen gegen Gasverluste
Die Hydrostatik befasst sich mit dem Verhalten ruhender Flüssigkeiten und den Kräften, die sie auf umgebende Körper ausüben. Im Maschinenbau spielt sie eine zentrale Rolle, besonders in Anwendungen, bei denen es auf verlustarme Kraftübertragung, minimale Reibung und hohe Lebensdauer ankommt. Durch den gezielten Einsatz hydrostatischer Prinzipien lassen sich Lager und Dichtungen entwickeln, die ohne direkten metallischen Kontakt arbeiten. Der erzeugte Flüssigkeitsfilm stabilisiert den Spalt zwischen den Bauteilen, indem er Lasten gleichmäßig verteilt und Gasdruck auf effiziente Weise abdichtet. Auf diese Weise werden sowohl Verschleiß als auch Energieverluste auf ein Minimum reduziert, was zu einer erheblichen Effizienzsteigerung und verlängerten Standzeiten führt.
Besonders in den hochbelasteten Bauteilen von Verbrennungsmotoren – etwa in spezialisierten Kurbelwellenlagern, Nockenwellensteuerungen, Wellendichtungen und Kolbenringen – entfalten diese hydrostatischen Prinzipien ihre Vorteile. Sie minimieren Reibungsverluste, verringern
thermische Belastungen und gewährleisten eine präzise Funktion, selbst unter extremen Betriebsbedingungen wie hohen Lagerbelastungen und stark schwankendem Gasdruck.
In diesen Anwendungen wird der Flüssigkeitsfilm nicht nur zur Reduktion des Verschleißes genutzt, sondern auch, um Gasverluste und Leckagen zu verhindern, wodurch die Effizienz des gesamten Systems optimiert wird.
Diese Lösung findet vor allem in modernen Hochleistungsmotoren mit hohen Anforderungen an Genauigkeit und Belastbarkeit Anwendung, da die Implementierung hydrostatischer Systeme eine zusätzliche Komplexität und externe Druckversorgung erfordert.
Hydrostatische Prinzipien basieren auf der gezielten Nutzung von Flüssigkeitsdruck zur Lastaufnahme und Abdichtung. Entscheidend dabei ist, dass sich der für diese Funktionen erforderliche Druck im Spalt nicht allein durch eine externe Druckquelle einstellt, sondern maßgeblich durch die Relativgeschwindigkeit zwischen den Bauteilen beeinflusst wird. Durch die Bewegung der Oberflächen entsteht im Spalt eine strömungsinduzierte Druckverteilung, die für die Tragfähigkeit und Dichtwirkung des Flüssigkeitsfilms essenziell ist.
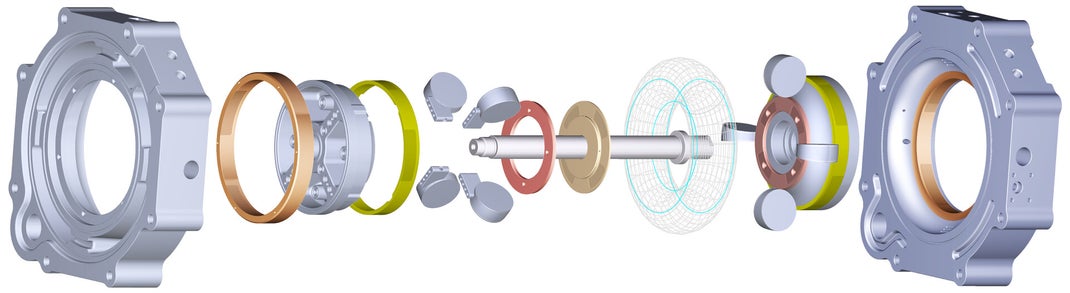
Die Explosionsdarstellung in Bild 24 zeigt den Antriebskern eines Rotationskolbenmotors (überarbeitete Generation) mit dem
integrierten hydrodynamischen Dichtungspaket.
In einem hydrostatischen Lager bewirkt die Relativbewegung zwischen der Welle und der Lagerbuchse, dass Öl in den engen Spalt strömt und dort einen Druckanstieg erfährt. Dieser Druckaufbau resultiert aus einer Kombination von hydrodynamischen und hydrostatischen Effekten. Während der hydrostatische Druck durch eine externe Pumpe vorgegeben wird, entsteht der eigentliche lasttragende Druckfeldverlauf durch die Relativgeschwindigkeit der Welle, die das Öl mitzieht und durch Quetschströmung zu einem Druckmaximum formt. Dadurch kann die Flüssigkeit die Lasten aufnehmen und die Welle von der Lagerbuchse trennen, wodurch metallischer Kontakt vermieden wird. Entscheidend für die Funktion ist die genaue Gestaltung des Spaltes, da die Druckverteilung von Faktoren wie Spaltdicke, Viskosität des Öls und Relativgeschwindigkeit abhängt.
Auch in hydrostatischen Dichtungen spielt dieser geschwindigkeitsabhängige Druckaufbau eine zentrale Rolle. Hier liegt auf einer Seite des Spalts der Gasdruck an, der durch die Dichtung zurückgehalten werden muss, während auf der anderen Seite ein gesteuerter Öldruck anliegt.
Durch die Relativbewegung der Bauteile entsteht eine strömungsinduzierte Druckverteilung innerhalb des Flüssigkeitsfilms, die eine zusätzliche Dichtwirkung erzeugt. Die Dichtung arbeitet somit nicht nur durch den statischen Öldruck, sondern besonders durch den durch die Bewegung entstehenden dynamischen Druckaufbau im Spalt. Ohne diese Relativgeschwindigkeit würde kein stabiler Flüssigkeitsfilm entstehen, der eine effektive Abdichtung gewährleistet.
Besonders vorteilhaft ist, dass der Öldruck auf der Niederdruckseite des Spalts gezielt gesteuert werden kann, um das Druckgefälle optimal an die Betriebsbedingungen anzupassen. Dies ermöglicht eine exakte Kontrolle über die Dichtwirkung, ohne dabei unnötige Reibungsverluste oder erhöhte Leckagen zu verursachen. Die Kombination aus extern geregeltem Öldruck und strömungsbedingtem Druckaufbau im Spalt sorgt somit für eine hochwirksame Abdichtung, die Gasverluste minimiert und die Standzeit der Komponenten maximiert.
Diese enge Wechselwirkung zwischen hydrostatischen und hydrodynamischen Effekten ist der Schlüssel zur Funktion solcher Systeme. Während der externe Druck für eine konstante Grundlastaufnahme sorgt, wird die eigentliche Tragfähigkeit und Abdichtwirkung erst durch die Relativbewegung der Bauteile erreicht. Hydrostatische Lager und Dichtungen nutzen diesen Effekt, um sowohl Reibung als auch Leckagen zu minimieren und so die Effizienz und Lebensdauer von Maschinen erheblich zu verbessern.
Dämpfungsmechanismus hydrostatischer Dichtungen bei
pulsierenden Belastungen
Ein weiterer entscheidender Vorteil hydrostatischer Dichtsysteme ist ihre Fähigkeit, pulsierende Relativgeschwindigkeiten und schwankende Gasdrücke zu dämpfen. Dies geschieht durch die spezifischen physikalischen Eigenschaften des Öls, insbesondere durch dessen Viskosität und Masse, die es ermöglichen, schnelle Druckänderungen abzupuffern und Schwingungen zu
absorbieren.
Bei pulsierenden Gasdrücken auf einer Seite des Spalts und einer oszillierenden Bewegung der angrenzenden Bauteile wirken hydrostatische Dichtungen wie ein hydraulischer Dämpfer. Das Öl im Spalt reagiert auf Druckänderungen mit einer verzögerten Strömungsanpassung, da es durch seine Viskosität Energie aufnimmt und Schwingungen abbaut. Die Flüssigkeit verhält sich dabei ähnlich wie eine federnde und dämpfende Masse, wodurch kurzfristige Druckspitzen nicht direkt an die Dichtungsflächen weitergegeben werden. Dadurch bleibt der Flüssigkeitsfilm stabil und verhindert auch unter stark schwankenden Bedingungen eine unkontrollierte Leckage.
Besonders bei Frequenzen im Bereich von 30 Hz bis 150 Hz, wie sie im Verbrennungsmotor durch Kolbenbewegungen und Druckschwankungen auftreten, zeigt sich diese Dämpfung als sehr effektiv. Die Resonanzfrequenz des Flüssigkeitsfilms liegt meist weit über diesem Bereich, sodass keine gefährlichen Eigenresonanzen auftreten, sondern die Druckschwankungen effizient absorbiert werden.
Zusätzlich kann durch eine gezielte Steuerung des Öldrucks der Dämpfungseffekt weiter optimiert werden. Eine adaptive Öldruckregelung erlaubt es, den hydrostatischen Film so anzupassen, dass er auch bei variierenden Betriebsbedingungen stabil bleibt. Damit lässt sich eine gleichmäßige Abdichtung mit minimalen Gasverlusten sicherstellen, selbst bei hohen Lastwechseln oder schnellen Drehzahländerungen.
Durch diese Kombination aus Viskositätsdämpfung, Massenträgheit des Öls und steuerbarer Öldruckregelung wird die Dichtwirkung auch unter extremen Betriebsbedingungen zuverlässig aufrechterhalten. Das macht hydrostatische Dichtungen besonders geeignet für Anwendungen, bei denen sowohl hohe als auch schwankende Gasdrücke auftreten, wie etwa bei Kolbenringen, Wellendichtungen und Ventilstegen in leistungsstarken Verbrennungsmotoren.
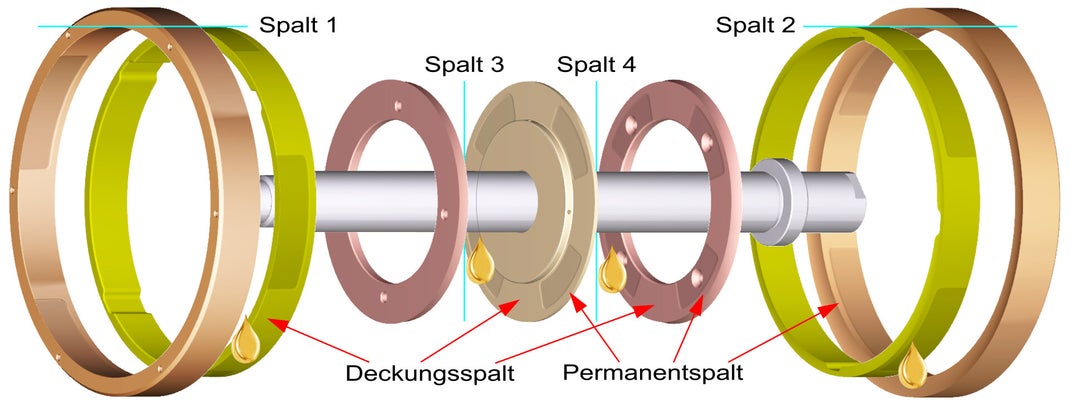
Die Explosionsdarstellung in Bild 25 zeigt das hydrodynamische Dichtungspaket eines Rotationskolbenmotors (überarbeitete Generation).
Die Spalte 1 und 2 entstehen durch Ringpaarungen. Ihre strukturierte Spaltoberfläche besteht aus einem durchgehenden Permanentspaltbereich sowie vier
45°-Deckungsspalten, die um jeweils 90° versetzt angeordnet sind.
Die Spalte 3 und 4, die durch Scheibenpaarungen gebildet werden, folgen demselben strukturierten Aufbau.
Die Schnittdarstellung in Bild 26 zeigt den Antriebskern eines Rotationskolbenmotors (überarbeitete Generation).
Die Spalte 1 und 2 (Ringpaarungen) weisen eine hohe Umlaufgeschwindigkeit auf, sodass die Spalthöhe etwas größer gewählt werden kann. Im Gegensatz dazu unterliegen die Spalte 3 und 4 (Scheibenpaarungen) einer geringeren Umlaufgeschwindigkeit, weshalb ihre Spalthöhe entsprechend kleiner ausfällt.
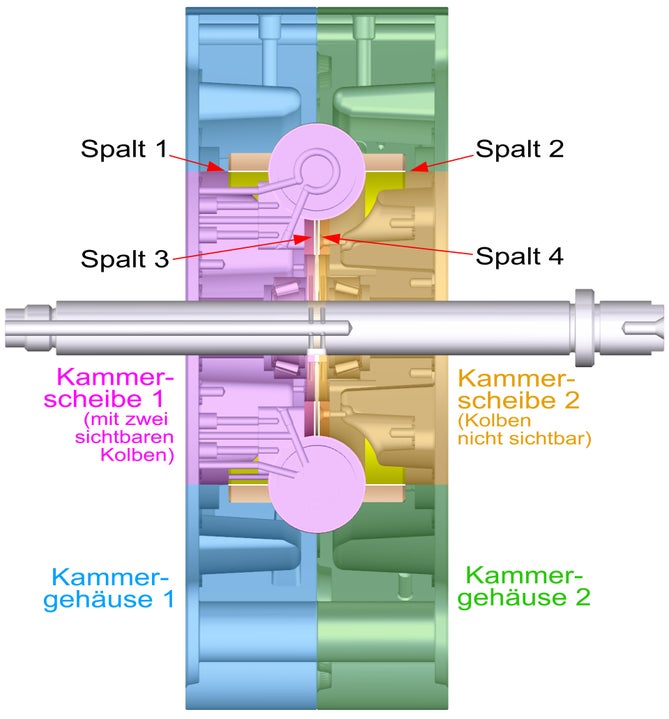
Die Architektur des Rotationskolbenmotors erfordert eine spezielle Abdichtung, um Gasverluste zu minimieren. Zwei Kammerscheiben rotieren innerhalb ihrer jeweiligen Kammergehäuse in einem dynamisch wechselnden Prozess (detallierte Erklärung - siehe Thema 1).
Zur Ermöglichung dieser Bewegung entstehen insgesamt vier Spalte:
(siehe Bild 25 und Bild 26)
Spalte 1 und 2 werden durch Ringpaarungen gebildet.
Spalte 3 und 4 entstehen durch Scheibenpaarungen.
Die Relativgeschwindigkeiten der Kammerscheiben zu den Kammergehäusen variieren dynamisch und sind abhängig von der Abtriebswellengeschwindigkeit, multipliziert mit dem Geometrieabhängigen Übersetzungsverhältnis zwischen 0 und 2,41.
Um Reibungsverluste bei diesen wechselnden Relativbewegungen zu minimieren, sind die Spalte strukturiert aufgebaut.
Ein schmaler Permanentspaltbereich erstreckt sich über die gesamten 360° der Ringe und Scheiben. Zusätzlich sorgen vier Deckungsspalte, die sich jeweils über 45° erstrecken und in 90°-Abständen angeordnet sind, für eine gleichmäßige Verteilung. Durch jeden Winkelschritt entstehen neue Spaltflächen, die sich kontinuierlich an das dynamische Übersetzungsverhältnis anpassen.
Die Animation in Bild 27 veranschaulicht den Deckungsverlauf der Spalte. Während der Permanentspalt eine durchgehende Abdichtung gewährleistet, überlappen sich die Deckungsspalte im kritischen Geschwindigkeitsbereich vollständig.
Dies ist besonders im Umkehrpunkt von Bedeutung, wo die Relativgeschwindigkeit
für wenige Millisekunden gegen
Null tendiert.
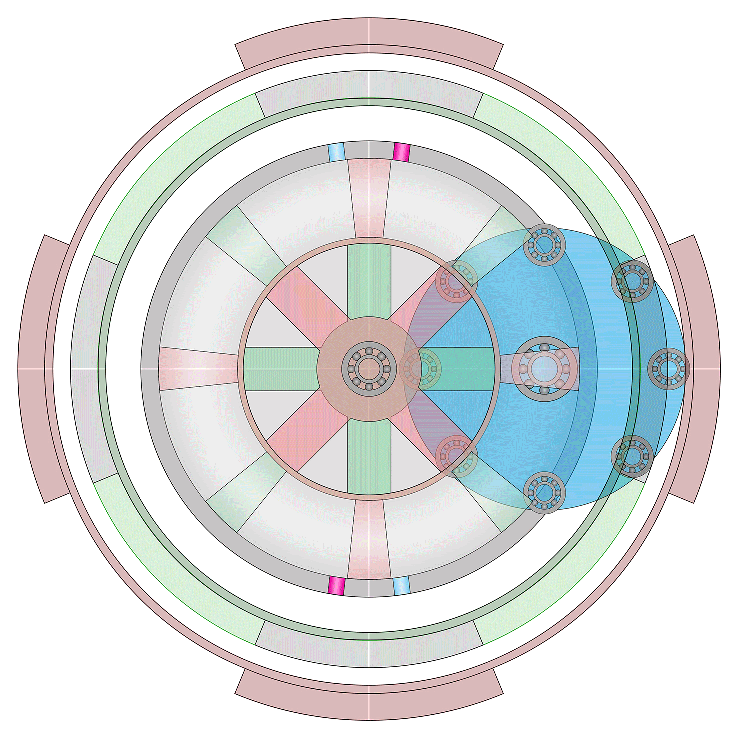
Technische Daten zur
Spaltgeometrie
Beide Spalthöhen (Ringspalt und Scheibenspalt)
befinden sich in einem unkritischen Fertigungs-
bereich und stellen keine konstruktive
Herausforderung im Maschinenbau dar.
Öl-Pumpendruck: 1bar
dynamische Viskosität: 0,015Pas (10W-40 bei 100°C)
Permanentspalttiefe: 3mm
Deckungsspalttiefe: 17mm
Spalthöhe Ringspalt: 0,035mm
Spalthöhe Scheibenspalt: 0,030mm
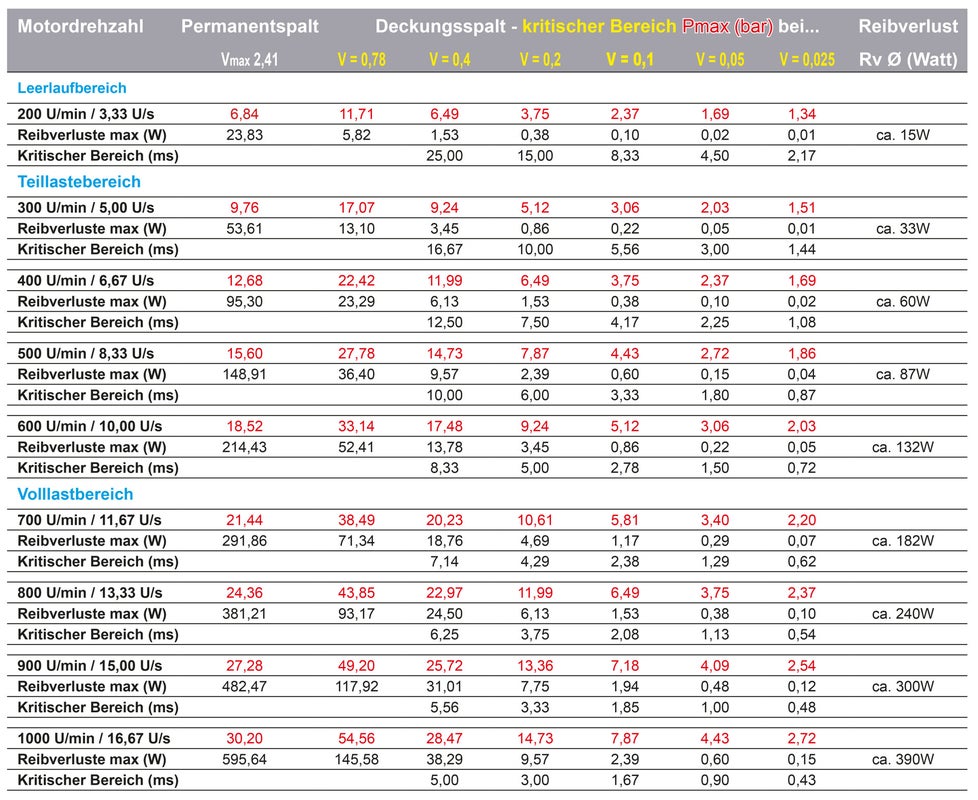
Die Tabelle in Bild 28 zeigt die hydrodynamischen Spaltdrücke (Rote Zahlen) in Abhängigkeit von den
Relativgeschwindigkeiten. Zudem sind die ungefähren Reibverluste in Watt sowie die entsprechenden Überbrückungszeiten über den kritischen Arbeitsbereich angegeben.
Die Grafik in Bild 29 zeigt einen vergrößerten Halbausschnitt des kritischen Arbeitsbereichs.
Der Graph veranschaulicht die Geschwindigkeitsabnahme in Abhängigkeit von der Winkelstellung zum Umkehrpunkt.
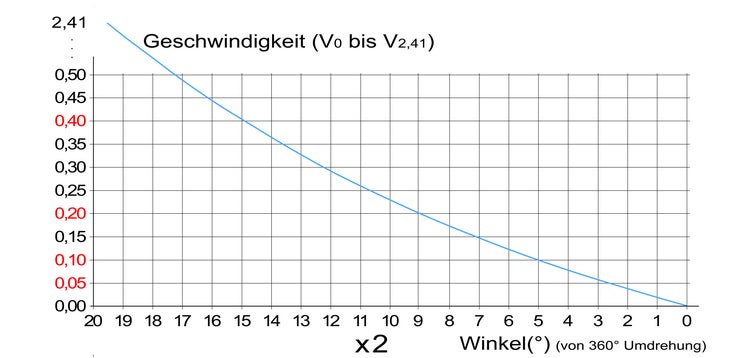
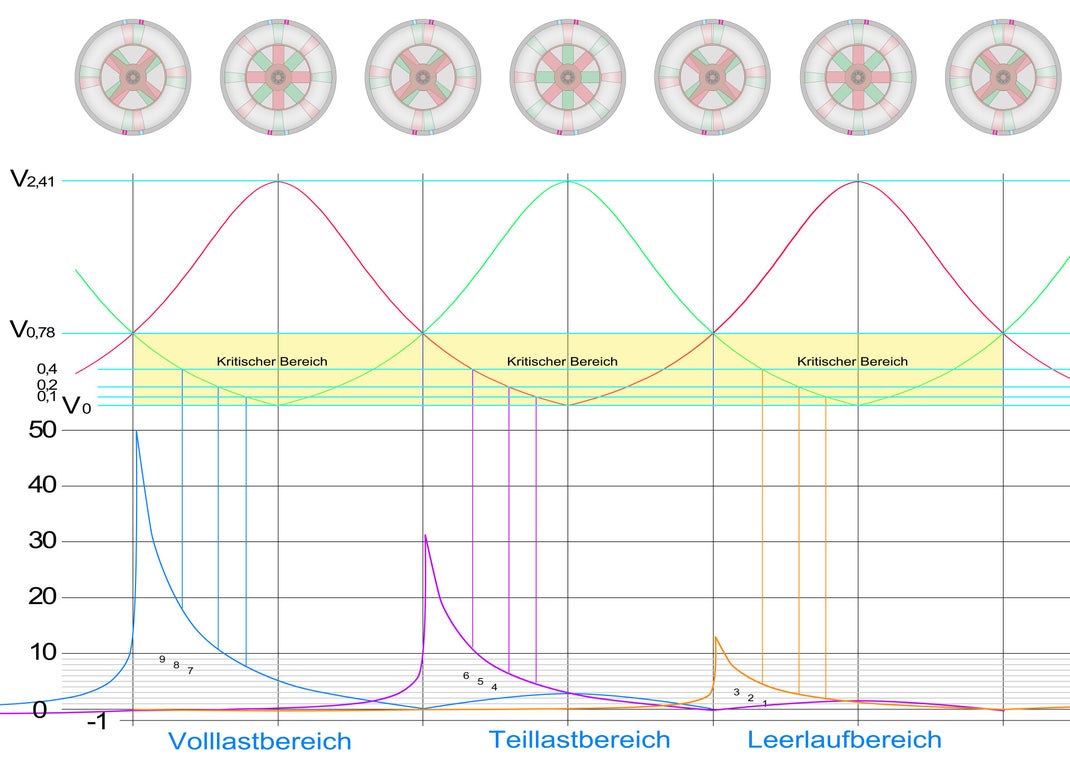
Die Grafik in Bild 30 veranschaulicht den Geschwindigkeitsverlauf der beiden Kammerscheiben 1 und 2 (dargestellt durch die rote und grüne Linie), die in einer Phasenverschiebung von 45° zueinander abgebildet sind. Beide Steuerscheiben rotieren in die gleiche Drehrichtung. Für die Funktion der hydrodynamischen Dichtung ist die präzise Gestaltung des Spaltes entscheidend, da die Druckverteilung von Faktoren wie der Spalthöhe, der Viskosität des Öls und der Relativgeschwindigkeit abhängt.
Die Relativgeschwindigkeiten der Kammerscheiben im Verhältnis zum Kammergehäuse sowie der Ringspalt- und Scheibenspaltpaarungen erreichen in bestimmten Phasen einen kritischen Bereich. Unmittelbar nach dem oberen Totpunkt (OT) wird durch die Zündung des Gasgemisches der höchste Expansionsdruck erzeugt. Dieser Expansionsdruck fällt schnell ab, muss jedoch durch den geschwindigkeitsabhängigen Spaltdruck ausreichend zurückgehalten werden, um das Öl im Spalt zu stabilisieren und den Brennraum gegen Gasverluste abzudichten.
Die Tabelle in Bild 28 zeigt die ungefähren Spaltdrücke Pmax in bar in den kritischen Bereichen für die Übersetzungsverhältnisse von 0,78 bis 0,025. Diese Eckwerte sind mit der Drehzahl der Abtriebswelle in neun verschiedenen Drehzahlbereichen (von 200 U/min bis 1000 U/min) multipliziert worden. Diese Ergebnisse decken die Spaltdrücke für den Leerlauf-, Teillast- und Volllastbereich ab. Vergleicht man die Spaltdruckwerte aus der Tabelle mit den Expansionsdruckwerten aus der Grafik in Bild 30, lässt sich feststellen, dass die Spaltdruckwerte den Expansionsdruckwerten vollständig standhalten können.
Diese sehr kurzen kritischen Zeitabschnitte (Überbrückungszeiten V<0,05) liegen zwischen 2,17 ms bei 200 U/min und 1,34 bar Expansionsdruck sowie 0,43 ms bei 1000 U/min und 2,72 bar Expansionsdruck. Diese Werte liegen deutlich unter 10 ms und stellen somit sicher, dass Gasverluste effektiv verhindert werden.
Der absolute Stillstand der Relativgeschwindigkeit im Umkehrpunkt des kritischen Bereichs wird durch die dämpfenden Trägheitseigenschaften des hydrodynamischen Dichtsystems ausreichend kompensiert.
Fazit und Ausblick
Die Geschichte des Verbrennungsmotors ist eng verknüpft mit zwei dominierenden Prinzipien: dem klassischen Hubkolbenmotor und dem einzigartigen Wankelmotor. Der Hubkolbenmotor hat sich seit seiner Erfindung im 19. Jahrhundert als unerschütterlicher Begleiter in Fahrzeugen, Flugzeugen und vielen Maschinen etabliert. Der Wankelmotor, geboren aus einer anderen Denkweise, brachte mit seiner Drehbewegung einen innovativen Ansatz – kompakter, leiser und theoretisch effizienter. Doch beide Konzepte standen vor großen Herausforderungen: der Thermodynamik, dem Verschleiß und der optimalen Systemintegration. Erst später rückte der Begriff Energieeffizienz zunehmend in den Mittelpunkt.
Mit wachsendem Fokus auf Effizienz und Steuerbarkeit gewann die präzise Kontrolle der Thermodynamik immer mehr an Bedeutung. Doch aufgrund ihrer Bauweise stoßen beide Systeme an Grenzen, wenn es darum geht, die ideale Expansion und Kompression der Verbrennungsgase zu erreichen – ein entscheidender Faktor, der den Wirkungsgrad maßgeblich beeinflusst. Dennoch vereinen beide Technologien sowohl Stärken als auch Schwächen.
Der neuartige Rotationskolbenmotor verspricht nun einen frischen technischen Ansatz, der darauf abzielt, die Thermodynamik gezielter und verlustärmer in mechanische Energie umzuwandeln. Ein Vergleich der drei Technologien mit ihren jeweiligen Vor- und Nachteilen könnte Aufschluss darüber geben, ob diese neue Verbrennungsmotortechnologie das Potenzial hat, mit den etablierten Prinzipien der Klassiker zu konkurrieren – oder sie womöglich zu übertreffen.
Ein objektiver Vergleich der Vor- und Nachteile des neuen Rotationskolbenmotors ist derzeit nur begrenzt möglich, da klassische Verbrennungsmotoren über Jahrzehnte optimiert wurden und den aktuellen Stand der Technik widerspiegeln. Der neuartige Rotationskolbenmotor befindet sich hingegen noch in der konzeptionellen Entwicklungsphase, und es fehlen bisher empirische Testreihen oder Messdaten, die eine fundierte Bewertung ermöglichen. Erst mit den ersten Prototypen werden sich belastbare Vergleichsmöglichkeiten herauskristallisieren.
Trotzdem ist es sinnvoll, bereits im konzeptionellen Stadium einen ersten Vergleich anzustellen, indem bekannte physikalische Prinzipien und bestehende technische Errungenschaften herangezogen werden. So lässt sich beispielsweise das Zusammenspiel von Kolben, Kolbenringen und Zylindern, das in diesem neuen Motortyp ähnlich gestaltet ist, auf Dichtigkeit, Machbarkeit und Effizienz beurteilen. Dieses gesamt überschaubare Wissen bietet wertvolle Anhaltspunkte für eine erste Bewertung. Wenn sich in der Gesamtbetrachtung vielversprechende Ansätze zeigen, kann der Weg für eine gezielte Weiterentwicklung geebnet werden.
Die nachfolgende Vergleichstabelle verdeutlicht die jeweiligen Stärken und Schwächen der drei Antriebskonzepte, die sich durch ihre spezifischen Konstruktionsprinzipien und technologischen Eigenschaften voneinander unterscheiden.
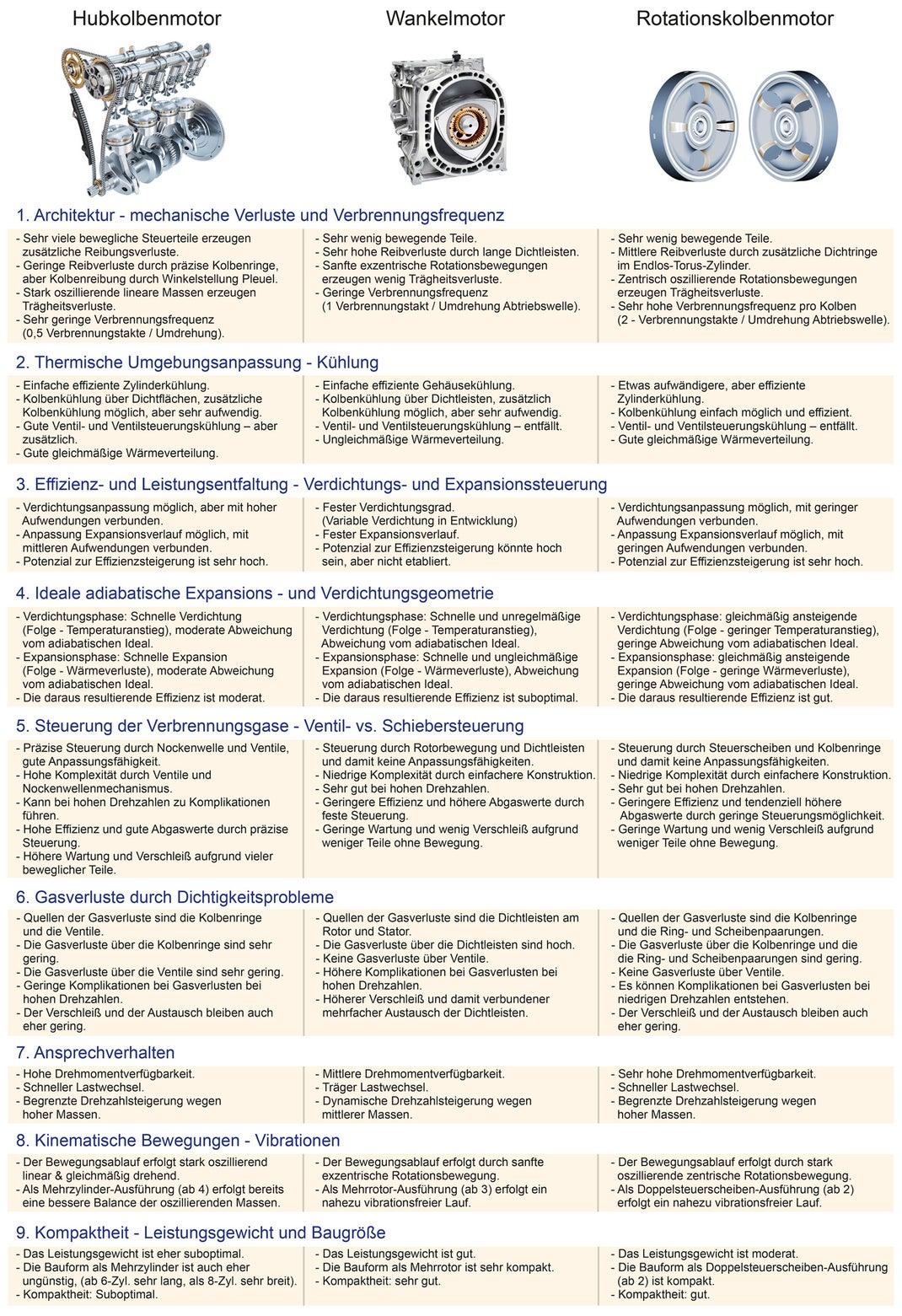
Der Wankelmotor zeigt seine größten Stärken in Laufruhe und kompakter Bauweise, was ihn ideal für Anwendungen mit hohen Drehzahlen und geringem Leistungsgewicht macht. Er findet vor allem in Sportwagen, Drohnen oder als Range-Extender in Elektrofahrzeugen Einsatz, wo er als kompakter Generator zur Reichweitenverlängerung dient.
Der Hubkolbenmotor überzeugt durch seine hohe Effizienz, eine präzise Ventilsteuerung und sein direktes Ansprechverhalten im Alltag. Seine robuste und zuverlässige Bauweise sowie die jahrzehntelange Optimierung seiner Abgaswerte machen ihn weiterhin zur dominierenden Antriebsform in Fahrzeugen, Maschinen und industriellen Anwendungen.
Der neue Rotationskolbenmotor kombiniert viele dieser Stärken der klassischen Antriebe und ergänzt sie um entscheidende Verbesserungen: zwei Verbrennungstakte pro Kolben für eine höhere Leistungsdichte, eine ideale Bewegungsgeometrie (Relativgeschwindigkeit des Kolbens) für eine temperaturstabilere, gleichmäßigere und damit effizientere Verdichtung und Verbrennung, eine regelbare beidseitige Kolbenkühlung sowie eine optimierte Verdichtungsventilsteuerung – und das alles in einer kompakten Bauweise mit minimalem Bauteilaufwand. Diese Kombination ermöglicht eine leichte, aber leistungsstarke Lösung mit höherer Effizienz.
Dank dieser Eigenschaften eignet sich der Rotationskolbenmotor besonders für hybride Antriebssysteme sowie leistungsstarke und kompakte Anwendungen in Hochleistungsfahrzeugen, Luftfahrttechnik und mobilen Generatoren. Seine kompakte Bauweise und das geringe Leistungsgewicht machen ihn zudem attraktiv Boote, Motorräder und alternative Antriebskonzepte, bei denen Effizienz, Platzersparnis und Laufruhe entscheidend sind.
Die Entwicklung dieses neuen technologischen Ansatzes eröffnet nicht nur Potenziale für Effizienzsteigerungen, sondern kann auch etablierte Denkmuster hinterfragen und weitere alternative Wege aufzeigen. Unser Konzept des Rotationskolbenmotors steht exemplarisch für die Möglichkeit, Verbrennungsmotoren mit innovativen Lösungen weiterzuentwickeln und sie in eine mögliche umweltfreundlichere Zukunft zu führen.
Mit dieser konzeptionellen Ausarbeitung dieses neuartigen Antriebsprinzips haben wir dargelegt, dass technologische Innovationen nicht zwangsläufig im Widerspruch zur Nachhaltigkeit und zum Klimaschutz stehen müssen. Im Gegenteil: Sie können entscheidend dazu beitragen, bestehende Herausforderungen zu lösen und eine mögliche neue Perspektive für nachhaltige Mobilität zu eröffnen.
Doch Innovation endet nicht auf dem Papier. Um den tatsächlichen Mehrwert dieses technischen Ansatzes zu belegen, haben wir bereits mit der Entwicklung eines ersten Prototyps begonnen. Dabei ist uns bewusst, dass die Umsetzung einer derart umfangreichen Technologie in den Prozess zukünftiger Technologien einzubinden nicht nur einen ersten Prototyp mit technischen Ergebnissen benötigt. Es fordert vielmehr interdisziplinäre Zusammenarbeit mit Fachleuten, die den Zugang zu spezialisierten Laboren und modernen Fertigungseinrichtungen haben und die vor allem über den gemeinsamen Willen verfügen, an zukunftsweisenden Technologien zu arbeiten.
Aus diesem Grund suchen wir gezielt den Austausch mit der Auto- und Zuliefererindustrie, Forschungseinrichtungen und politischen Akteuren. Eine enge Zusammenarbeit mit Unternehmen und Hochschulen kann dazu beitragen, die praktische Machbarkeit weiter zu verfeinern, während politische Rahmenbedingungen den Weg für eine technologieoffene Zukunft ebnen könnten.
Unser Konzept steht außerdem als ein Beispiel dafür, dass Fortschritt nicht durch pauschale Verbote entsteht, sondern durch gezielte Innovation. Die Zukunft der Mobilität liegt nicht in der Einschränkung von Möglichkeiten, sondern in der Weiterentwicklung bestehender und neuer Technologien.
Dipl.-Ing. Axel Schnippering